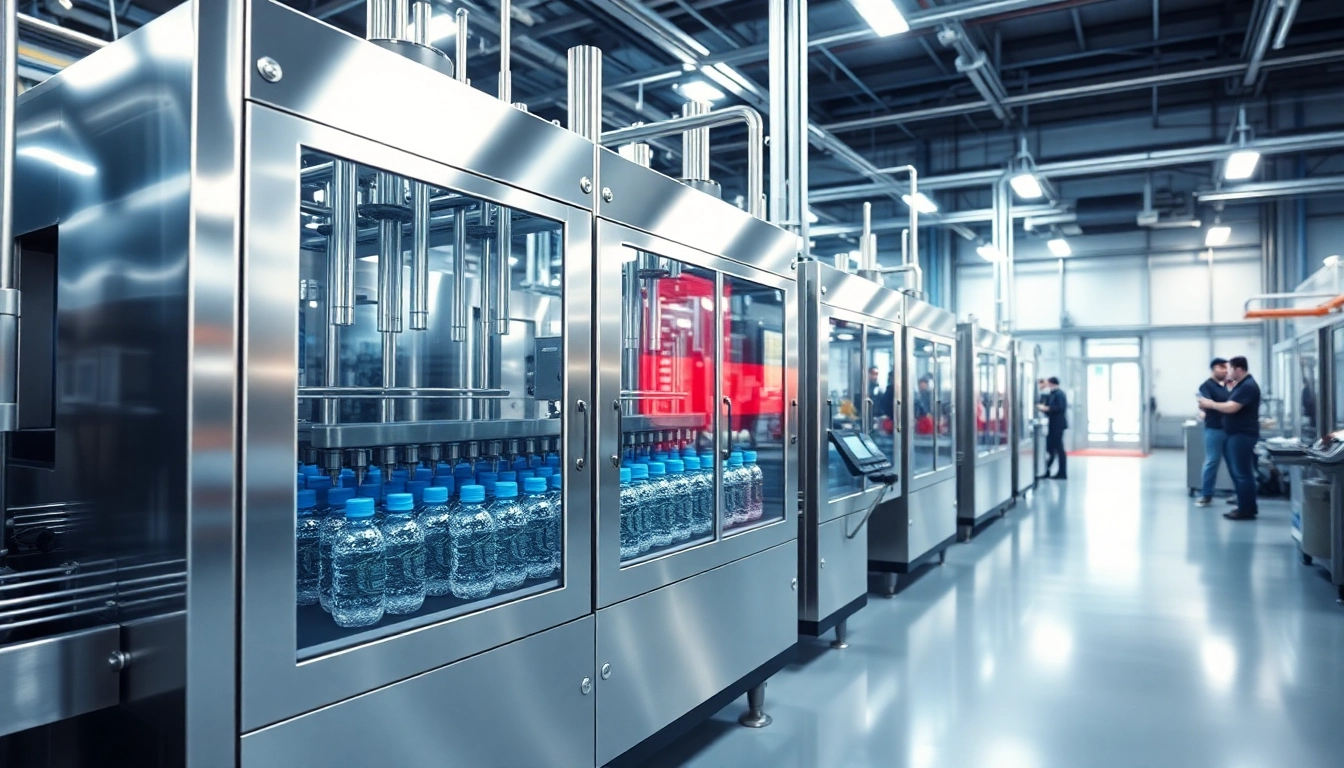
Top Liquid Packaging Machine Supplier: Enhance Your Production Efficiency
Understanding Liquid Packaging Machines
In the dynamic landscape of industrial production, Liquid Packaging Machine Suppliers play a crucial role in optimizing operational efficiency. These machines are designed to handle the complex task of packaging liquid products across various industries, ensuring that goods are securely contained and ready for distribution. In this comprehensive guide, we delve deep into the world of liquid packaging machines, exploring their types, applications, and the factors to consider when selecting a supplier.
What is a Liquid Packaging Machine?
A liquid packaging machine refers to specialized equipment used to package liquid products into a variety of containers, such as bottles, pouches, or cartons. These machines are vital in sectors such as food and beverage, pharmaceuticals, cosmetics, and chemicals. The primary functions of liquid packaging machines include filling, sealing, and labeling, allowing manufacturers to automate the packaging process efficiently.
Types of Liquid Packaging Machines
Liquid packaging machines come in various configurations, each designed for specific liquid types and packaging requirements. Some of the notable types include:
- Filling Machines: These machines fill containers with precise volumes of liquid. They can be further classified into piston fillers, gravity fillers, and vacuum fillers, each serving different product viscosities.
- Capping Machines: Once filled, the containers are capped using automatic or semi-automatic capping machines that ensure tight seals to preserve the quality of the liquid.
- Labeling Machines: To enhance brand recognition and provide product information, labeling machines apply stickers or print labels onto containers as they move away from the filling line.
- Cartoning Machines: These machines are used for packaging products into boxes or cartons, ensuring safe transit of the packaged goods.
Applications Across Industries
The versatility of liquid packaging machines means they are applicable in multiple sectors:
- Food and Beverage: This includes packaged drinks, sauces, soups, oils, and dairy products. High-speed and hygienic packaging solutions are essential in this industry.
- Pharmaceuticals: Liquid packaging machines ensure that medications, syrups, and other medicinal liquids are packaged securely, often under stringent regulatory guidelines.
- Cosmetics: Products like shampoos, conditioners, and lotions require aesthetically pleasing packaging that liquid packaging machines can provide efficiently.
- Chemicals: This sector often deals with hazardous liquids requiring special handling and safe packaging solutions to prevent leaks or spills.
Choosing the Right Supplier
Selecting a liquid packaging machine supplier is a pivotal decision for any manufacturer. Various factors influence this choice, all of which play a crucial role in long-term operational success.
Key Factors in Supplier Selection
When evaluating potential suppliers, consider the following factors:
- Experience and Expertise: Assess the supplier’s experience in your specific industry, as this can significantly impact the quality and reliability of the equipment they provide.
- Technology and Innovation: Look for suppliers that leverage cutting-edge technology to enhance efficiency and reduce downtime.
- Customization Options: Suppliers who offer tailored solutions can address specific packaging challenges, providing machinery configured to meet unique operational needs.
- Customer Support: Ensure the supplier has robust support services, including training, maintenance, and spare parts availability.
Evaluating Quality and Reliability
Quality and reliability are paramount in the selection of a liquid packaging machine supplier:
- Quality Certifications: Verify if the supplier’s equipment meets industry standards and possesses relevant certifications, ensuring that they comply with international quality regulations.
- Durability: Assess the materials used in the machine’s construction. Machines built with high-quality materials are more likely to withstand continuous operation and require less maintenance.
- User Reviews and Testimonials: Investigate feedback from previous clients to gauge the supplier’s reputation and the efficacy of their machines in real-world applications.
Comparison of Leading Suppliers
In the competitive landscape of liquid packaging, several suppliers stand out:
- Accutek Packaging Equipment: Known for their wide range of filling machines suitable for various products.
- IPharmachine: Offers specialized solutions, such as the DXD-80Y automatic liquid packaging machine, designed for diverse industries.
- Liquid Packaging Solutions: Renowned for their custom machinery designed to meet individual business needs.
Cost Considerations
Understanding the cost implications of procuring liquid packaging machines is essential for budgeting and financial planning.
Budgeting for Your Liquid Packaging Machine
When budgeting for a liquid packaging machine, consider:
- Initial Investment: This includes the cost of purchasing the machine itself, installation fees, and any necessary modifications to existing lines.
- Operating Costs: Evaluate ongoing costs such as maintenance, parts replacement, and energy consumption.
- Training Costs: Don’t overlook potential training costs associated with getting staff acquainted with new machinery.
Cost vs. Value: Making an Informed Decision
It’s important to weigh the cost against the value provided:
- Efficiency Gains: Consider how the new machine will enhance productivity and possibly lower labor costs in the long run.
- ROI Expectations: Calculate the return on investment based on increased production capacity and reduced wastage.
- Long-Term Reliability: Lower-priced machines may result in higher long-term costs due to repairs and inefficient operations.
Financing Options Available
If upfront costs are a concern, explore various financing options:
- Leasing: Leasing equipment can reduce initial financial burden and allows for easy upgrades in the future.
- Loans: Many suppliers offer financing plans that allow you to spread the cost over several months or years.
- Grants and Subsidies: Research potential grants or subsidies available for businesses investing in technology upgrades or efficiency improvements.
Implementation and Integration
Successfully integrating a new liquid packaging machine into your production line requires careful planning and execution.
Steps to Implement Your Packaging Solution
To implement the new equipment effectively:
- Site Assessment: Evaluate the current production site to determine the best location for the machine, ensuring proper workflow and accessibility.
- Installation: Work closely with the supplier for correct installation and initial setup to avoid future operational issues.
- Testing: Conduct extensive testing to ensure the machine operates correctly and meets production specifications before full-scale implementation.
Training Staff on New Equipment
Training is crucial for maximizing the machine’s performance:
- On-Site Training: Arrange for supplier representatives to provide hands-on training to your staff to familiarize them with operations and safety protocols.
- Develop Standard Operating Procedures (SOPs): Put in place clear SOPs to guide staff in operating and maintaining the machine.
- Continuous Learning: Encourage ongoing training sessions to adapt to any updates or enhancements to the machine technologies.
Maintenance Best Practices
Regular maintenance extends the lifespan of your liquid packaging machine:
- Routine Inspections: Implement a schedule for routine inspections to identify any issues before they escalate into costly repairs.
- Cleaning Protocols: Establish hygiene protocols especially in food and pharmaceutical applications to prevent contamination.
- Documentation: Maintain records of all maintenance and repairs, which can be helpful for warranty claims and future troubleshooting.
Future Trends in Liquid Packaging
The packaging industry is ever-evolving, and staying informed about future trends will help businesses remain competitive.
Technological Innovations on the Horizon
As technology advances, liquid packaging is set to benefit from various innovations:
- Automation: Increased automation using AI and robotics to enhance precision and reduce labor costs.
- Smart Packaging: Integration of IoT to create smart packaging solutions that track inventory and monitor product conditions in real-time.
- Custom Packaging: Advances in customization technologies permitting tailored packaging solutions for unique products.
Environmental Impact and Sustainability
Environmental sustainability is becoming a focal point in the packaging industry:
- Recyclable Materials: A shift towards using recyclable and biodegradable materials to reduce environmental footprints.
- Reduced Waste: Optimizing packaging processes to minimize waste and enhance resource efficiency.
- Energy-Efficient Machines: Suppliers are starting to offer machines that significantly reduce energy consumption over their lifetime.
Preparing for Market Changes
To stay ahead, manufacturers need to be adaptable:
- Market Research: Conducting market research to identify trends and shifts in consumer preferences helps in timely adjustments.
- Flexibility: Investing in versatile machines that can handle various liquid types and packaging sizes can provide a competitive advantage.
- Collaboration: Building partnerships with suppliers who can offer not only machines but also insights into industry best practices and innovations.