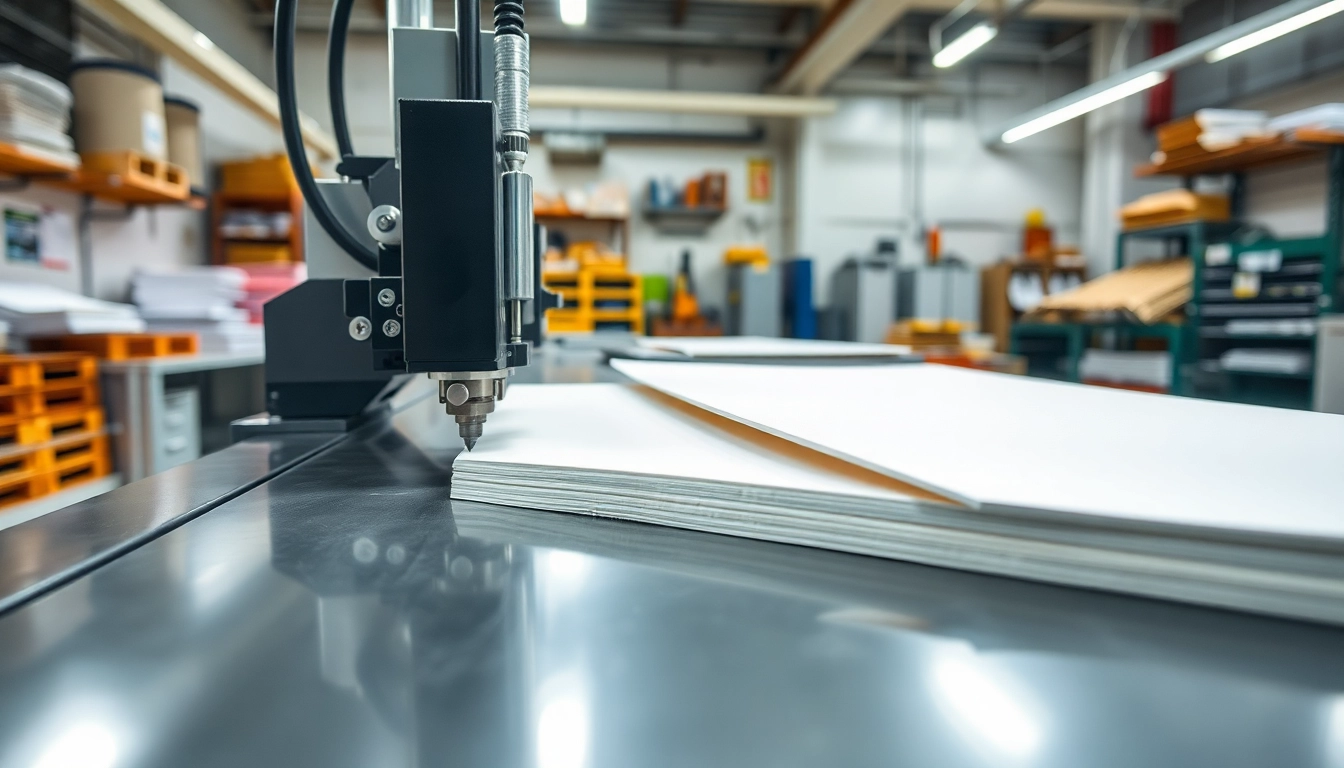
Precision Die Cutting: Optimizing Processes for Enhanced Quality and Efficiency
Understanding Precision Die Cutting
Definition and Importance of Precision Die Cutting
Precision die cutting is a specialized manufacturing process used to create intricate shapes and designs from various materials with exceptional accuracy. This technique employs sharp dies to cut, trim, or shape materials like paper, cardboard, foam, plastic, and metal into required specifications. It is pivotal across numerous industries, providing essential components and packaging solutions that meet rigorous standards.
The importance of precision die cutting lies in its ability to streamline production processes, enhance designs, and reduce waste. By producing consistent pieces with high precision, it ensures that every product meets the design specifications required while minimizing the need for further manual labor, which can introduce inaccuracies. Industries from automotive to consumer goods rely heavily on this methodology due to its efficiency and versatility for various applications. For further insights, you can explore more about precision die cutting.
Common Applications and Industries
Precision die cutting finds application in various sectors, including:
- Packaging: Businesses utilize precision die cutting for producing boxes, trays, and other packaging materials that require specific shapes for safety and branding purposes.
- Automotive: The automotive industry relies on die cutting for gaskets, seals, and liners that fit precisely in vehicles, ensuring performance and safety.
- Medical: In the medical field, custom components such as surgical instruments and protective equipment are manufactured with precision die cutting to meet strict regulatory standards.
- Electronics: Components for electronic devices often need to be cut from insulating materials, thermal management foams, or other substrates, requiring the high accuracy that precision die cutting delivers.
Overview of Precision Die Cutting Materials
Various materials can be used in precision die cutting, including:
- Papers and Boards: Commonly used for packaging, printing, and crafts.
- Plastics: Such as polycarbonate, acrylic, and polyethylene, used extensively in manufacturing and electronics.
- Foams: Employed in cushioning and insulation applications across industries.
- Metals: Thin metals, including aluminum and copper, are cut for electronic and automotive parts.
Types of Precision Die Cutting Techniques
Rotary vs. Flatbed Die Cutting
There are two primary techniques used in precision die cutting: rotary and flatbed. Each method has its unique advantages and applications.
- Rotary Die Cutting: This method employs a cylindrical die that rotates to cut materials as they pass through. It excels at high-speed production and is particularly suited for continuous roll material. Rotary die cutting is highly efficient for creating consistent shapes and is ideal for applications requiring high volumes of output, such as labels and packaging.
- Flatbed Die Cutting: In flatbed die cutting, the die is pressed against the material in a flat position. It is particularly versatile for thicker materials and can handle a wide range of shapes and sizes. Although it operates at a slower speed compared to rotary methods, flatbed die cutting is well-suited for short runs and custom projects, allowing for a higher degree of customization.
Digital Die Cutting: Advantages and Disadvantages
Digital die cutting represents an innovative approach that allows for enhanced flexibility and control in the die cutting process. This technique uses computer-controlled blades to cut materials based on digital designs.
Advantages:
- Flexibility: Digital die cutting allows for easy adjustments of designs, enabling rapid prototyping and customization.
- No Setup Cost: Unlike traditional methods, digital die cutting doesn’t require physical dies, eliminating setup costs for small batch runs.
- Precision: Offers high precision and repeatability, making it perfect for intricate designs.
Disadvantages:
- Speed: Digital die cutting may be slower than traditional methods for large volume production.
- Material Limitations: Some materials may not be suitable for digital cutting due to their thickness or density.
Choosing the Right Technique for Your Needs
Selecting the appropriate die cutting technique depends on several factors, including volume, material type, and the intricacy of the design. Businesses should consider the following:
- Assess the material type and thickness, whether it can be effectively cut by a specific method.
- Consider production volume, as high volumes might benefit from rotary die cutting, while custom or low-volume runs might be better suited for flatbed or digital techniques.
- Evaluate budget constraints and the cost-effectiveness of maintenance for the chosen technique.
Benefits of Precision Die Cutting
Cost Efficiency and Waste Reduction
One of the most significant benefits of precision die cutting is its cost efficiency. The process allows for:
- Reduced Material Waste: The ability to cut materials to exact specifications minimizes leftover scrap, leading to substantial cost savings.
- Lower Labor Costs: Automation in die cutting reduces the need for manual labor, streamlining production and operational costs.
Quality and Consistency in Production
Precision die cutting ensures that each piece produced meets stringent quality standards. Advantages include:
- Consistent Output: Automated precision cutting produces identical parts with minimal variance, vital for applications that require uniformity.
- Enhanced Quality Control: The process typically integrates quality checks at various stages, ensuring that any deviations are caught early in the production line.
Improved Turnaround Times and Scalability
Rapid production capabilities of precision die cutting facilitate quick turnaround times necessary for fulfilling market demands:
- Fast Production Speeds: Techniques like rotary die cutting allow for rapid processing, essential for high-demand situations.
- Scalability: The process can efficiently scale production runs to meet increasing demand without a significant investment in time or resources.
Best Practices for Precision Die Cutting
Choosing the Right Materials for Cutting
Selecting the proper materials is crucial in precision die cutting. Factors affecting material choice include:
- Material Thickness: Ensuring the material is compatible with the chosen die cutting method.
- Adhesive Properties: Some materials may require specialized adhesives to achieve the desired bonding.
- Environmental Resistance: Consideration of environmental factors such as temperature and humidity that may impact material performance.
Maintenance and Calibration of Die Cutting Machines
Regular maintenance and calibration of die cutting machines are essential to ensure optimal performance:
- Scheduled Maintenance: Implementing routine checks and maintenance schedules can prevent downtime and costly repairs.
- Calibration: Machines should be calibrated regularly to maintain precision and ensure that cuts meet exact specifications.
Implementing Quality Control Measures
Quality control should be integrated throughout the die cutting process:
- Pre-Production Testing: Conduct tests using sample runs to identify potential issues before full production.
- In-Process Inspections: Regular inspections during the cutting process help maintain quality and catch errors early.
Future Trends in Precision Die Cutting
Technological Innovations in Precision Die Cutting
As industries evolve, the demand for precision die cutting will continue to grow, with emerging technologies influencing the process:
- Integration of Artificial Intelligence: AI is expected to bring about advancements in design optimization and machine operation, enhancing precision.
- 3D Die Cutting: The advent of 3D technologies will allow for more complex designs that traditional methods struggle to achieve.
Shifts in Market Demand and Applications
With trends leaning towards sustainability, there’s a growing demand for environmentally friendly materials in precision die cutting, influencing industry practices:
- Sustainable Materials: Increased market interest in biodegradable and recyclable materials will impact product offerings.
- Customization Demands: As consumers increasingly seek personalized products, companies must adapt their die cutting processes to meet changing demands.
Environmental Considerations and Sustainability Practices
The industry is seeing a push towards sustainability in precision die cutting:
- Waste Reduction: Incorporating strategies to reduce waste in the production process.
- Energy Efficiency: Investing in machines that consume less energy, thereby reducing the environmental footprint.