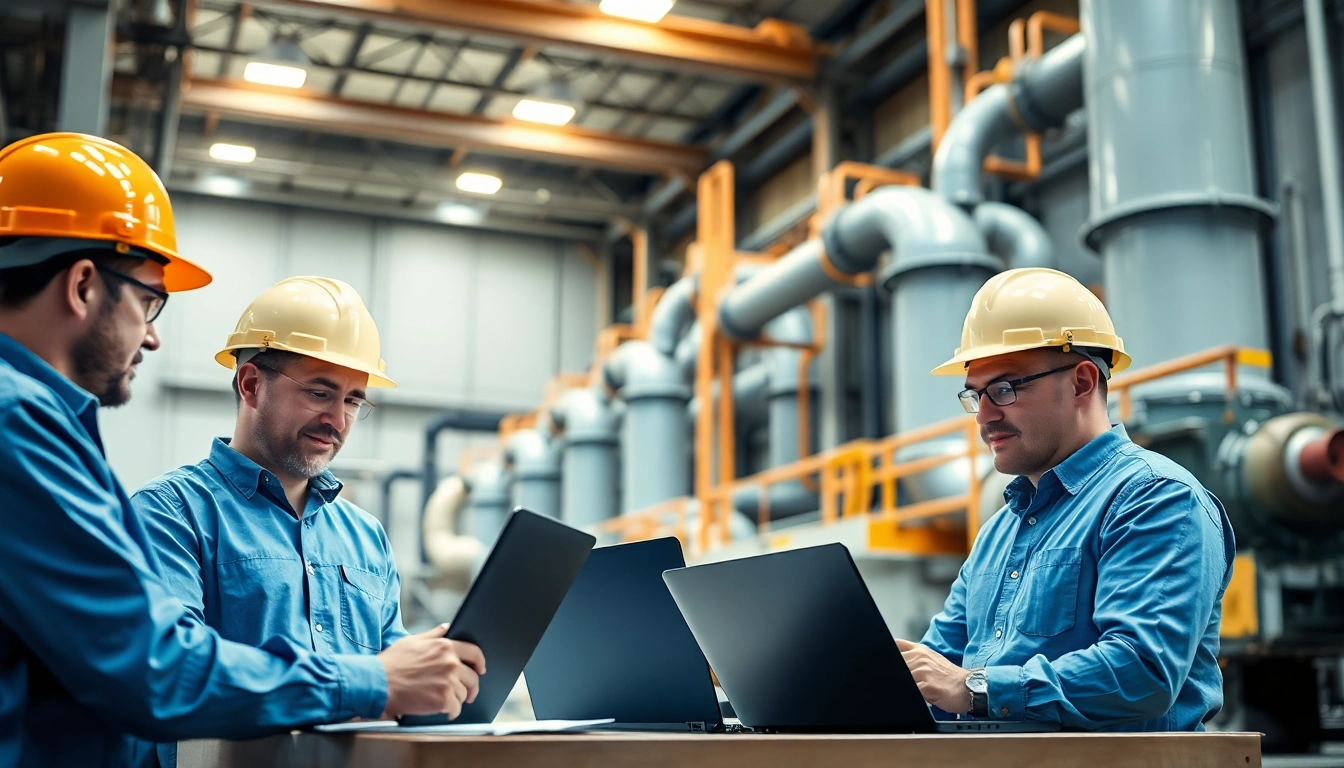
Piping Stress Analysis: Comprehensive Solutions from a Leading Piping Stress Company
The Importance of Pipe Stress Analysis in Engineering
In the engineering world, ensuring the integrity and safety of piping systems is paramount. As industries expand and develop, the complexity of piping systems increases, making effective piping stress analysis a vital discipline. Organizations seeking to enhance their operational efficiency often look to a piping stress Company for specialized solutions that ensure compliance with industry standards while safeguarding equipment and personnel. This article explores the fundamental aspects of pipe stress analysis, its significance, and how organizations can benefit from it.
What is Pipe Stress Analysis?
Pipe stress analysis is a comprehensive evaluation process designed to determine the effects of weight, thermal expansion, pressure, and environmental variables on a piping system. By analyzing the specific conditions of the piping system, engineers can ensure that the design can withstand expected loads without structural failure or functional issues. This evaluation typically utilizes advanced engineering software that adheres to industry standards, allowing for precise calculations and assessments.
Key Benefits of Stress Analysis for Piping Systems
1. Safety and Reliability: The primary benefit of conducting a pipe stress analysis is enhancing the safety and reliability of the piping system. By identifying potential stress points and weaknesses, preventative measures can be initiated before issues arise.
2. Cost Savings: Effective stress analysis helps avoid costly downtime and repairs, as it allows companies to address vulnerabilities proactively. By ensuring that systems are properly engineered from the start, organizations can save financial resources.
3. Regulatory Compliance: Industries such as oil and gas, chemical processing, and power generation must adhere to strict regulations. Conducting thorough stress analyses ensures compliance with standards such as ASME B31, leading to safer operations and reduced legal liability.
Common Applications of Pipe Stress Analysis in Industry
Pipe stress analysis forms an integral part of various industries, including:
- Oil and Gas: Ensuring the integrity of pipelines that transport hazardous materials is critical. Stress analysis helps to mitigate risks associated with leaks and bursts.
- Chemical Processing: In this sector, maintaining consistent flow and preventing malfunctions in the piping systems are of utmost importance. Stress analysis ensures that systems can withstand chemical reactions and their resulting thermal changes.
- Power Generation: Pipes that transport steam or other fluids must endure high pressures and temperatures. Stress analysis assists in designing systems that can handle these extreme conditions without failure.
- Manufacturing: Diverse manufacturing processes depend on piping systems to facilitate production. Effective pipe stress analysis can enhance efforts to optimize production and reduce risk.
Understanding Stress Factors in Piping Systems
Mechanical Loads and Their Impact on Piping
Mechanical loads exert force on piping systems primarily due to the weight of the pipes, insulation, added equipment, and the transported contents. Different types of mechanical loads can significantly affect the integrity of a piping system:
- Dead Loads: The weight of the pipeline itself and any permanent fixtures, like valves and fittings.
- Live Loads: Dynamic loads, such as movement due to equipment operation or changes in the working environment.
- Thermal Loads: Temperature changes cause materials to expand and contract, creating stress within the system.
Thermal Expansion: A Critical Consideration
Thermal expansion is a significant factor in piping systems, particularly those that operate under varying temperature conditions. When liquids or gases inside the pipes heat up, they expand; this can create pressure on the pipe walls and fittings, leading to high-stress conditions. A well-executed pipe stress analysis considers thermal expansion coefficients and their implications, allowing for the incorporation of expansion loops or other mitigating measures in the design phase.
How Vibration Affects Pipe Integrity
Vibration, whether from surrounding machinery or fluctuations in fluid flow, can contribute to pipe stress. Continuous exposure to vibrations can lead to fatigue and failure over time. Stress analysis incorporates vibration analysis to ensure that the piping system remains resilient under operational pressures. Solutions may include utilizing vibration dampeners, adjusting support spacings, and incorporating materials that can withstand dynamic movements.
Engineering Principles Behind Piping Stress Analysis
Fundamental Theories of Stress Distribution
Understanding the behavior of materials under stress is essential for engineers engaged in pipe stress analysis. The fundamental theories focus on how stress distributes across a system, which can be influenced by several factors, including:
- Material Properties: Different materials react uniquely to stress based on their elasticity, tensile strength, and overall characteristics.
- Geometry of Components: The shape and size of pipes and fittings affect how stresses are distributed throughout the piping system.
Comprehending these principles informs decision-making regarding material selection and design adaptations, ensuring operational efficacy and safety.
ASME Codes and Standards for Piping
Adherence to established codes and standards is vital in piping design and analysis. The American Society of Mechanical Engineers (ASME) provides several guidelines, such as:
- ASME B31.1: Covers power piping and is critical for the power generation sector.
- ASME B31.3: Pertains to process piping and is widely used in the chemical and petroleum industries.
- ASME B31.5: Addresses refrigerant piping, a crucial aspect in HVAC systems.
Compliance with these codes ensures that piping systems meet safety, performance, and reliability expectations.
Using Software for Accurate Stress Calculations
The modern piping stress analysis process increasingly relies on specialized software solutions that provide accurate calculations and simulations. Software such as CAESAR II and AutoPIPE enable engineers to model complex systems, including:
- Thermal expansion conditions
- Dynamic response to operational changes
- Load analysis for various scenarios
Utilizing advanced software in the analysis process not only accelerates the evaluation time but also improves accuracy, thereby facilitating more informed and reliable design choices.
Choosing the Right Piping Stress Company for Your Needs
What to Look for in a Pipe Stress Analysis Provider
Selecting the right piping stress company is critical to the success of any project. Here are some factors to consider:
- Reputation: Investigate the company’s history, client testimonials, and case studies to gauge their reliability.
- Technical Expertise: Consider the qualifications and experience of the engineers who will be involved in your project.
- Service Range: Ensure the company can provide comprehensive services, from initial design through to analysis and support.
Evaluating Expertise and Experience in the Field
Evaluating a company’s experience may include reviewing their portfolio of completed projects, particularly those similar to your own needs. Direct communication with their engineers can also provide insights into their problem-solving approaches and responsiveness.
Understanding Service Offerings and Technology Used
Different piping stress analysis companies utilize various technologies and methodologies. It is important to comprehend the tools they use and ensure they align with industry standards. Companies who embrace advanced computational technologies generally yield more precise and efficient results.
Success Stories: Case Studies of Effective Pipe Stress Analysis
Real-World Application of Stress Analysis Techniques
There are numerous instances where effective pipe stress analysis has positively impacted projects across different sectors. A notable example comes from a major oil and gas company’s investment project. By employing a thorough stress analysis during the design phase, potential failures were identified, leading to modifications that saved the company several million dollars in anticipated future repair costs.
Lessons Learned from Industry Challenges
Learning from industry challenges is crucial. An example comes from a chemical processing facility where a failure resulted from inadequate stress analysis. The incident prompted a complete review of their analytical processes and reinforced the importance of stringent evaluation methods.
Future Trends in Piping Stress Analysis
The future of piping stress analysis lies in the advancement of technology. Expect to see:
- Increased Automation: More automated evaluation processes will enhance accuracy and reduce manual labor.
- Advanced Simulation Techniques: Real-time simulations will allow engineers to monitor stress and optimize performance dynamically.
- Integration of IoT: Smart piping systems integrated with IoT technology will provide ongoing monitoring and data analysis, improving predictive maintenance.