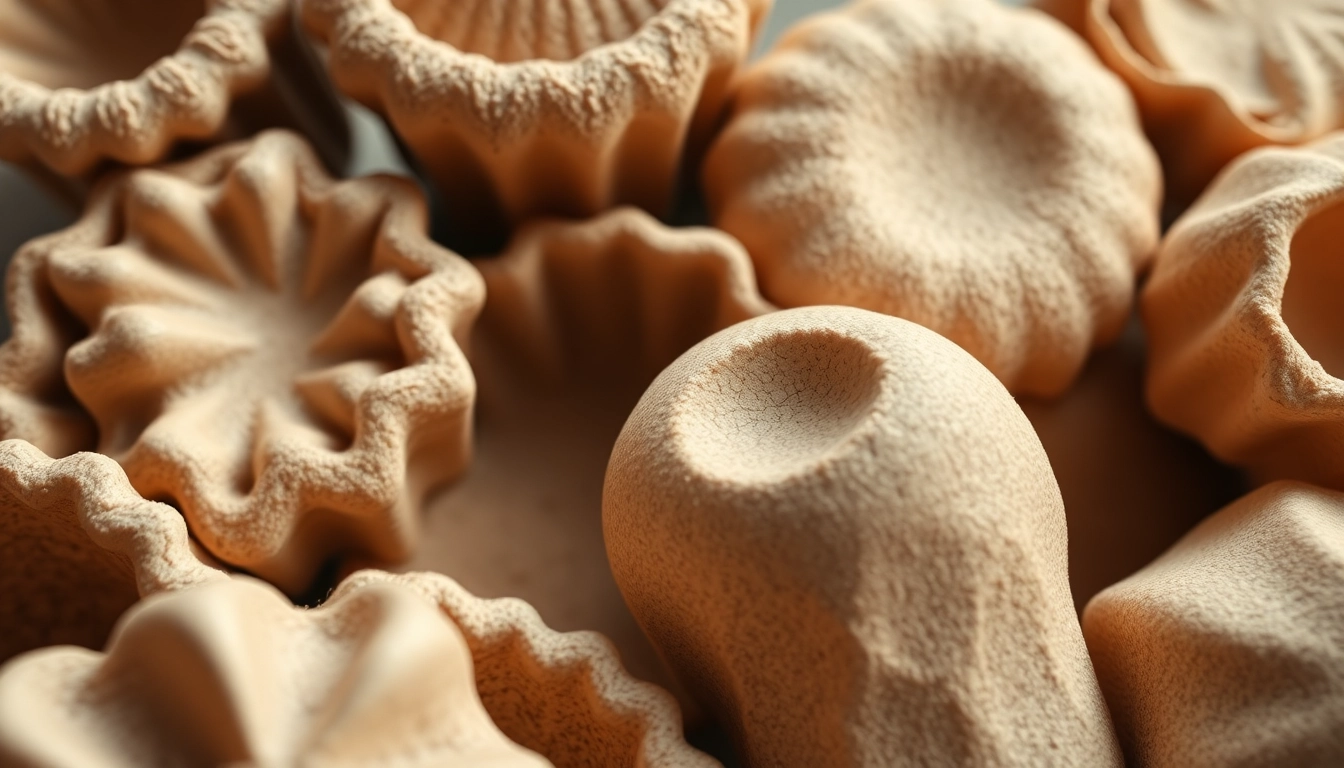
Molded Pulp Products: Sustainable Packaging Solutions for a Greener Future
Understanding Molded Pulp Products
What are Molded Pulp Products?
Molded pulp products, also referred to as molded fiber or molded pulp, are eco-friendly packaging materials primarily made from recycled paperboard and newsprint. This sustainable packaging solution is gaining popularity across various industries due to its versatility, effectiveness in protecting items, and minimal environmental impact. Molded pulp is created through a meticulous process of forming, drying, and producing functional packaging options that cater to diverse needs. Unlike traditional plastic and foam packaging, molded pulp offers a biodegradable alternative that retains structural integrity while being environmentally responsible. For businesses transitioning to greener solutions, molded pulp products provide an opportunity to enhance their brand image and fulfill sustainability commitments.
Types of Molded Pulp Products
Molded pulp products come in various forms, each designed to serve specific purposes. The common types include:
- Trays: Used extensively for consumer goods, food items, and electronics, trays can be designed with compartments for multiple products.
- Inserts: These provide protective cushioning for fragile items during shipping, ensuring they reach their destination without damage.
- Containers: Ideal for foods, beverages, and take-out services, these containers are fully compostable and act as a sustainable alternative to conventional plastic containers.
- Custom Designs: Many manufacturers offer the option to create custom molded pulp products tailored to specific business needs, enhancing branding while ensuring product safety.
Benefits of Using Molded Pulp
The advantages of using molded pulp products extend beyond just cost-effectiveness. Some compelling benefits include:
- Sustainability: As a renewable resource, molded pulp is biodegradable and recyclable, making it a better choice for eco-conscious consumers and corporations.
- Cost-Effectiveness: Although initial costs can be higher compared to cheaper packaging options, molded pulp products often reduce shipping costs due to their lightweight nature and efficient stacking ability.
- Protective Qualities: Molded pulp provides cushioning and shock absorption, effectively safeguarding products from environmental hazards during transport.
- Customizability: Brands can create tailored designs to enhance product presentation and differentiate themselves in competitive markets.
Applications of Molded Pulp Products
Consumer Electronics Packaging
In the consumer electronics sector, molded pulp products are utilized for packaging delicate items such as smartphones, tablets, and other gadgets. Their ability to absorb shocks and prevent movement during transit is crucial in protecting these fragile devices. Custom inserts can be engineered to fit the specific dimensions of the product, ensuring a snug fit that mitigates the risks of damage. This effectiveness not only enhances consumer trust but also positions brands as environmentally responsible players within the tech industry.
Food and Beverage Services
The food and beverage industry benefits greatly from molded pulp packaging, particularly in take-out and delivery services. Trays and containers made from molded pulp are perfect for carrying meals, as they provide an impermeable barrier to oil and moisture, ensuring that food remains fresh and appetizing. Additionally, being compostable, these products aid restaurants and food service providers in reducing their carbon footprint and appealing to eco-conscious customers.
Industrial Packaging Solutions
In industrial settings, molded pulp products are utilized for packaging machinery components, tools, and other equipment. By replacing traditional packaging methods that often involve plastic or foam, industries can streamline their operations while adhering to stricter environmental standards. The strength and durability of molded pulp make it an ideal candidate for shipping heavy and sensitive items without the risk of damage.
The Manufacturing Process of Molded Pulp
Materials Used in Production
The primary materials for producing molded pulp include recycled paper, cardboard, and sometimes natural fibers such as bamboo or sugarcane bagasse. The selection of materials plays a crucial role in the quality and properties of the final product, creating a sustainable circular approach that utilizes waste materials efficiently.
Steps Involved in Manufacturing
The manufacturing process of molded pulp involves several stages:
- Pulping: Recycled materials are collected and mixed with water, creating a slurry.
- Forming: The slurry is poured into a mold that defines the desired shape of the product. Vacuum pressure may be used to eliminate excess water.
- Drying: The formed product is transferred to drying equipment where air or heat is applied to evaporate moisture and harden the material.
- Finishing: The dried pulp products are trimmed, inspected for quality, and packaged for distribution.
Quality Control Measures
To achieve superior quality products, manufacturers implement rigorous quality control measures throughout the production process. This includes testing for durability, structural integrity, and adherence to environmental standards. Regular audits and metrics tracking ensure that each batch meets specific safety and performance standards before reaching the market.
Sustainability Advantages of Molded Pulp
Environmental Benefits
The environmental impact of molded pulp products is significantly lower compared to that of traditional plastic packaging. As a biodegradable material, molded pulp naturally decomposes, avoiding long-term waste in landfills. Moreover, using recycled materials in production further reduces the demand for new resources and lessens the carbon footprint associated with manufacturing.
Comparing Costs with Plastic Alternatives
While molded pulp products may sometimes require higher upfront investments, they often yield long-term savings. Businesses can benefit from lower shipping costs due to their lightweight nature and efficient space utilization during transport. Additionally, consumer preferences shifting toward eco-friendly options may result in increased brand loyalty and sales, making molded pulp a financially smart choice in the long run.
Recyclability and Biodegradability
One of the significant advantages of molded pulp products lies in their recyclability and biodegradability. Consumers are increasingly concerned about packaging waste, and offering products that can be composted or easily recycled meets this demand. Businesses using molded pulp packaging can enhance their sustainability profiles, fostering a positive image while encouraging responsible disposal among customers.
Choosing the Right Molded Pulp Supplier
Top Manufacturers in the Industry
Several companies stand out in the molded pulp manufacturing arena. Key players such as Henry Molded Products, Keiding, and Western Pulp Products specialize in providing high-quality, customized molded pulp packaging solutions catering to various sectors. Researching these suppliers can pave the way for forming robust partnerships aimed at sustainability and efficiency.
Criteria for Selection
When selecting a molded pulp manufacturer, businesses should consider the following criteria:
- Quality Assurance: Investigate the manufacturer’s quality control practices and certifications to ensure product standards are met.
- Customization Options: Look for flexibility in design and the ability to create tailored products that meet specific needs.
- Sustainability Practices: Evaluate the supplier’s own environmental policies and their sourcing of materials.
- Pricing and Delivery: Compare costs and delivery timelines to find a partner that aligns with your budget and schedule.
How to Get Custom Solutions
Obtaining custom molded pulp solutions involves a collaborative approach where businesses communicate their specific requirements to manufacturers. Initiating discussions about product dimensions, design intricacies, and material preferences will assist suppliers in delivering tailored solutions that meet your needs effectively. Prototyping options may also be available to test designs before full-scale production begins.