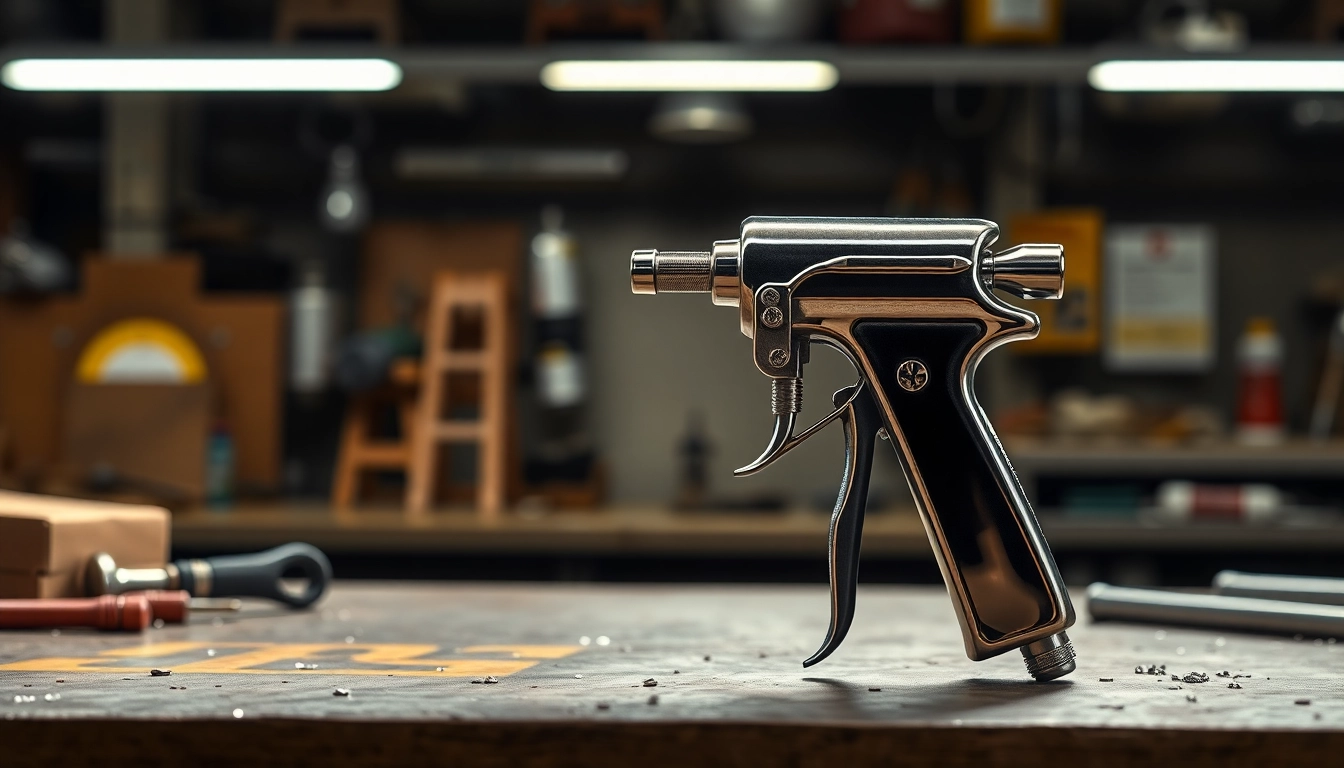
Maximize Efficiency in Metalworking with Top Needle Gun Techniques
Understanding Needle Guns: What You Need to Know
1. Definition and Functionality of Needle Guns
A needle gun, also known as a needle scaler, is a powerful tool designed primarily for surface preparation in metalworking applications. This device features multiple steel needles that move rapidly to create a hammering action. The key function of a needle gun is to remove various forms of surface contaminants such as rust, paint, and scale from metals, ensuring clean surfaces for subsequent processes such as painting or welding.
The needle gun’s operation relies on pneumatic or electric power, yielding significant advantages in terms of efficiency and speed. By utilizing pressurized air or an electric motor, these tools can deliver thousands of beats per minute (BPM), effectively dislodging stubborn materials without damaging the underlying surface. This makes needle guns particularly useful in industries such as automotive repair, shipbuilding, and construction.
2. Different Types of Needle Guns: Pros and Cons
When selecting a needle gun, it is essential to understand the different types available. The two primary classifications are pneumatic needle guns and electric needle guns.
Pneumatic Needle Guns
Pneumatic needle guns utilize compressed air to operate, making them lightweight and often more powerful. Some of their advantages include:
- High Power-to-Weight Ratio: Pneumatic models typically offer a superior power-to-weight ratio, making them suitable for heavy-duty tasks.
- Durability: These tools generally have fewer moving parts, which can lead to longer lifespans.
However, they also have downsides:
- Dependency on Air Supply: They require a reliable air compressor, which can limit portability.
- Noise Level: Pneumatic guns can be quite loud, necessitating ear protection.
Electric Needle Guns
Electric needle guns run on electricity and offer distinct advantages:
- Portability: Without the need for an air compressor, they can be taken anywhere and used at more locations.
- Quieter Operation: Generally, electric models operate with less noise, enhancing user comfort.
However, they have their cons:
- Weight: Often heavier due to the electric motor, which could make long-term use more cumbersome.
- Power Output: May not match the peak performance of pneumatic equivalents.
3. Common Applications in Metalworking
Needle guns find widespread application in various sectors due to their efficacy in surface preparation. Some notable applications include:
- Automotive Industry: Preparing metal surfaces before painting or repair, ensuring better adhesion.
- Shipbuilding: Removing rust and contaminants from vessels, particularly in hard-to-reach areas.
- Infrastructure Maintenance: Regular upkeep of metal structures, bridges, and equipment to extend lifespan and prevent failure.
Choosing the Right Needle Gun for Your Needs
1. Key Features to Consider
When selecting a needle gun, consider various features that will enhance its performance and suit your specific needs:
- Needle Count: More needles generally mean faster work, but consider the type of surface you’ll be working on.
- Stroke Speed: BPM ratings indicate how quickly the tool can operate; higher values are more efficient.
- Weight and Ergonomics: Lighter tools will be easier to handle, especially for prolonged tasks.
2. Air-Powered vs. Electric Needle Guns
The choice between air-powered and electric models often boils down to application context and personal preference. For heavy-duty industrial tasks, pneumatic options may excel, while electric tools might be favored for their portability in home workshops or light repairs.
3. Tips for Selecting a High-Quality Tool
To ensure you invest wisely in a needle gun:
- Brand Reputation: Research reputable brands with positive reviews. Brands like Ingersoll Rand and Powermate are commonly recommended.
- Warranty and Support: Check if the manufacturer offers a warranty and what customer support is available.
- Before Purchase Testing: Whenever possible, try a demonstration of the device to ensure it meets your performance expectations.
Proper Usage Techniques for Needle Guns
1. Safety Precautions When Using Needle Guns
Safety should always be your foremost concern when operating a needle gun. Here are essential precautions to consider:
- Personal Protective Equipment (PPE): Always wear safety goggles, ear protection, and a dust mask to protect against debris.
- Secure Work Environment: Ensure the area is well-ventilated and clear of unnecessary obstacles.
- Tool Maintenance: Regularly inspect the needle gun for faults or damages. Avoid using damaged tools.
2. Step-by-Step Guide for Effective Metal Surface Preparation
Using a needle gun effectively involves understanding the technique:
- Preparation: Clean the area of any loose materials or dust.
- Setting Up: Choose the right needle configuration based on the surface condition.
- Operation: Maintain a consistent distance from the surface for even scaling. Use steady, controlled movements.
- Finishing: After use, ensure the surface is clean and free from dust and debris.
3. Troubleshooting Common Issues
Even quality tools can encounter problems. Common issues include:
- Poor Performance: Often caused by clogged needles or insufficient air pressure for pneumatic tools. Regular cleaning and maintenance can resolve this.
- Excessive Vibration: This can occur if the needles are worn out; replacing them may solve the issue.
- Inconsistent Power: For electric models, check the power source and cord integrity; for pneumatic models, ensure that the air compressor is set correctly.
Maintenance Tips for Longevity of Your Needle Gun
1. Regular Cleaning and Care Practices
To maximize the lifespan of your needle gun, consistent maintenance is crucial:
- Cleaning: After every use, blow out any particles that may be lodged in the needles and housing.
- Lubrication: Apply lubrication as recommended by the manufacturer to prevent rust and ensure smooth operation.
- Needle Inspection: Regularly inspect needles for wear; replace them at the first sign of damage.
2. Identifying Wear and Tear
Signs of wear can include:
- Decreased Efficiency: If the tool underperforms, it may be time for maintenance or replacement.
- Physical Damage: Any visible cracks or breaks in the needles or housing indicate immediate replacement is necessary.
- Excessive Vibration: This often suggests needle wear or an issue within the machine itself.
3. Replacement Parts: When and How to Change
Replacement parts can significantly restore performance:
- Needles: Depending on usage, they may need replacement every few sessions or after heavy use.
- O-Rings and Seals: Inspect these every so often, as they can wear out, leading to air leaks in pneumatic models.
- Power Cords: Look for frays or cuts; ensure connections are secure, especially in electric models.
Advancements in Needle Gun Technology
1. Innovations in Design and Functionality
With technological advancements, needle guns have seen various innovations:
- Improved Ergonomics: Many new models are designed with user comfort in mind, featuring better grip and reduced weight.
- Variable Speed Settings: Some modern needle guns now come with adjustable settings, allowing for tailored performance depending on the task.
2. The Future of Needle Guns in Industrial Applications
As industries push for higher efficiency and safety standards, needle guns are likely to evolve further:
- Integration with Robotics: We may see automated systems that incorporate needle guns, improving precision and efficiency.
- Smart Technology: Future tools may incorporate IoT capabilities for real-time monitoring and data collection.
3. Customer Feedback and Market Trends
Market trends indicate a growing preference for brands that emphasize safety and innovation. Customer feedback suggests a demand for:
- Enhanced User Experience: Consumers are looking for lighter tools with better ergonomics.
- Durability: Quality materials that extend tool life are consistently rated highly.