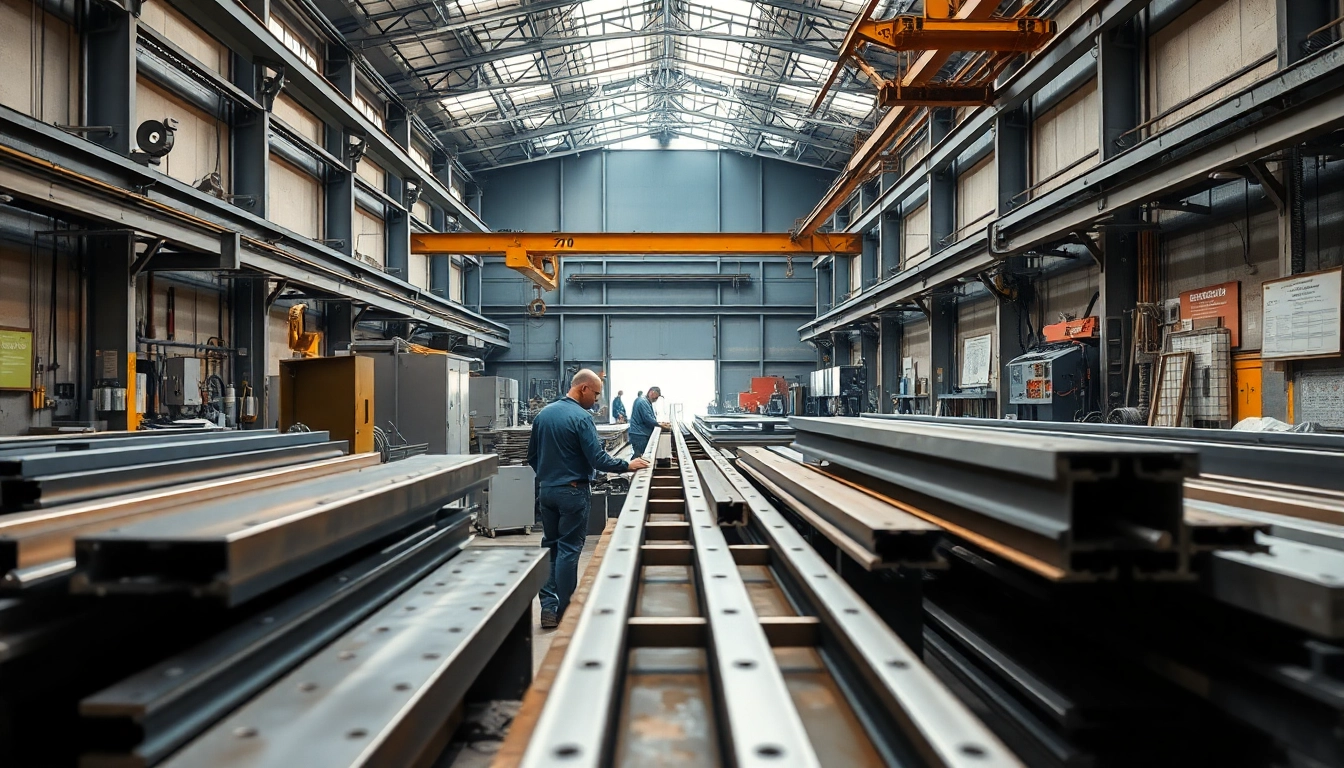
Leading the Metal Manufacturing Industry in Edmonton: Insights and Solutions
Understanding the Role of a Metal Manufacturer in Edmonton
Industry Overview and Trends
The metal manufacturing industry in Edmonton plays a critical role in the local economy, contributing significantly to sectors such as construction, transportation, and energy. With the rise of infrastructure projects and the growing demand for durable materials, the industry is evolving rapidly. Technological advancements, including automation and precision engineering, are transforming traditional practices and enhancing productivity. The implementation of innovative materials, such as lightweight alloys and composites, is also on the rise, reflecting the industry’s adaptability to market demands.
Key Services Offered by Metal Manufacturers
Metal manufacturers in Edmonton provide a range of services tailored to meet the diverse needs of their clients. These services often include:
- Metal Fabrication: The process of cutting, bending, and assembling metal parts to create structured components.
- Welding and Joining: Techniques used to fuse metal components together, essential for various assemblies and constructions.
- Precision Machining: Involves using advanced machinery to achieve highly accurate dimensions and finishes on metal parts.
- Metal Finishing: Enhancements such as coating, painting, or plating to improve durability and appearance.
- Custom Tooling: Creation of specialized tools and dies that cater to specific manufacturing needs.
Importance of Quality and Standards in Metal Manufacturing
Quality assurance is paramount in metal manufacturing. Adhering to industry standards not only ensures the integrity and safety of products but also builds trust with customers. Compliance with regulations such as ISO 9001 is essential for maintaining high-quality processes. Regular inspections, testing of materials, and continuous improvement initiatives are common practices adopted by reputable metal manufacturers. Investing in quality not only enhances product performance but also reduces waste and operational costs in the long run.
Finding the Right Metal Manufacturer in Edmonton
Factors to Consider when Choosing a Manufacturer
When searching for a metal manufacturer Edmonton, several critical factors must be evaluated to ensure a successful partnership:
- Experience and Reputation: Look for manufacturers with a solid track record and positive client testimonials.
- Capabilities and Technology: Assess the technology and capabilities the manufacturer has in relation to your specific needs.
- Certifications and Compliance: Ensure the manufacturer adheres to relevant industry standards and certifications.
- Customer Service: Responsive communication and support services indicate a customer-oriented business.
- Cost and Value: Although price matters, evaluate the value you receive in terms of quality and service.
Comparing Competitors in the Edmonton Area
Understanding the competitive landscape is crucial when selecting a metal manufacturer. Evaluating several manufacturers based on quality, pricing, and timelines can reveal significant insights. Utilize comparative analysis tools like SWOT analysis (Strengths, Weaknesses, Opportunities, Threats) to assess how different companies stack up against one another. This method will help identify which manufacturer best aligns with your project requirements and budget.
Tips for Evaluating Manufacturer Credentials
To effectively evaluate a metal manufacturer, consider the following tips:
- Request Certifications: Verify any claims regarding certifications and standards compliance.
- Visit Facilities: If possible, tour the manufacturing site to assess capabilities firsthand.
- Ask for References: Reach out to past clients to gain insights into their experiences.
- Review Case Studies: Analyze previous projects that reflect their experience in your specific area of need.
- Test Orders: Start with smaller orders to evaluate quality and service before committing to larger contracts.
Innovative Techniques in Metal Manufacturing
Emerging Technologies in the Industry
The metal manufacturing sector is at the forefront of technological innovation. Technologies such as 3D printing, which allows for rapid prototyping and production of intricate designs, are gaining traction. Advanced materials like titanium alloys and carbon fiber composites are reshaping manufacturing possibilities, enhancing strength without adding weight. Other innovations, such as artificial intelligence (AI) in production analytics and robotics in assembly processes, are contributing to increased efficiency and reduced labor costs.
Implementing Efficiency in Fabrication Processes
Improving efficiency in fabrication is crucial for staying competitive. Techniques like Lean Manufacturing and Just-In-Time (JIT) production reduce waste and optimize resources. By implementing these methods, manufacturers can lower costs and enhance production speeds. Using software solutions for project management and workflow automation also plays a significant role in streamlining operations, thereby minimizing delays and maximizing output.
Case Studies of Successful Metal Projects
Analyzing successful case studies provides valuable lessons and insights. For instance, a local manufacturer recently undertook a project to supply components for a major infrastructure development. By utilizing advanced fabrication techniques and materials, they delivered high-quality products ahead of schedule, significantly above industry standards. This not only reinforced their reputation but also opened new avenues for future contracts, essentially demonstrating the benefits of innovation and quality in metal manufacturing.
Ensuring Compliance and Sustainability
Understanding Local Regulations and Standards
Metal manufacturers must navigate an intricate landscape of local regulations and compliance standards. Staying informed about safety protocols, environmental regulations, and industry-specific requirements is essential for legal operation. Regular audits and compliance checks ensure adherence to local codes and practices. Keeping abreast of any changes to legislation can help manufacturers anticipate challenges and adapt proactively.
Eco-friendly Practices in Metal Manufacturing
With the growing emphasis on sustainability, many metal manufacturers are adopting eco-friendly practices. This may include the use of recycled materials, waste management programs, and energy-efficient production techniques. Implementing measures such as water recycling systems and solar energy dependence not only benefits the environment but can also lead to cost savings over time.
Benefits of Sustainable Manufacturing Solutions
Opting for sustainable practices has numerous advantages. Aside from complying with regulations, sustainable manufacturing can enhance a company’s brand image and attract environmentally conscious clients. Furthermore, sustainable approaches often lead to improved process efficiency and lower operational costs through waste reduction and resource optimization. Investing in sustainability helps build a resilient business that can thrive in a rapidly changing market.
Future of Metal Manufacturing in Edmonton
Potential Growth Areas for the Industry
The future of metal manufacturing in Edmonton looks promising, with several growth areas on the horizon. Advances in technology and increasing infrastructure projects, particularly in sectors such as renewable energy and transportation, will likely drive demand. Additionally, the shift towards automation and smart manufacturing can enhance productivity and expand market reach, providing metal manufacturers with new opportunities to explore.
Impact of Global Trends on Edmonton Manufacturers
Global trends such as digital transformation and globalization are influencing local metal manufacturers. With advancements in technology fostering connectivity, local manufacturers now have access to a broader market for exporting their products. Additionally, the demand for customized solutions based on global specifications allows Edmonton manufacturers to collaborate internationally, share knowledge, and adopt best practices from around the world.
Preparing for Industry Changes and Innovations
To remain competitive, metal manufacturers must be proactive in preparing for industry changes. This involves continuous education and training for the workforce, investment in cutting-edge technology, and adaptability to evolving market demands. Embracing a culture of innovation will be crucial for companies that wish to thrive in a dynamic environment. By staying ahead of trends and investing in research and development, manufacturers can position themselves as leaders in the industry, prepared for the challenges and opportunities that lie ahead.