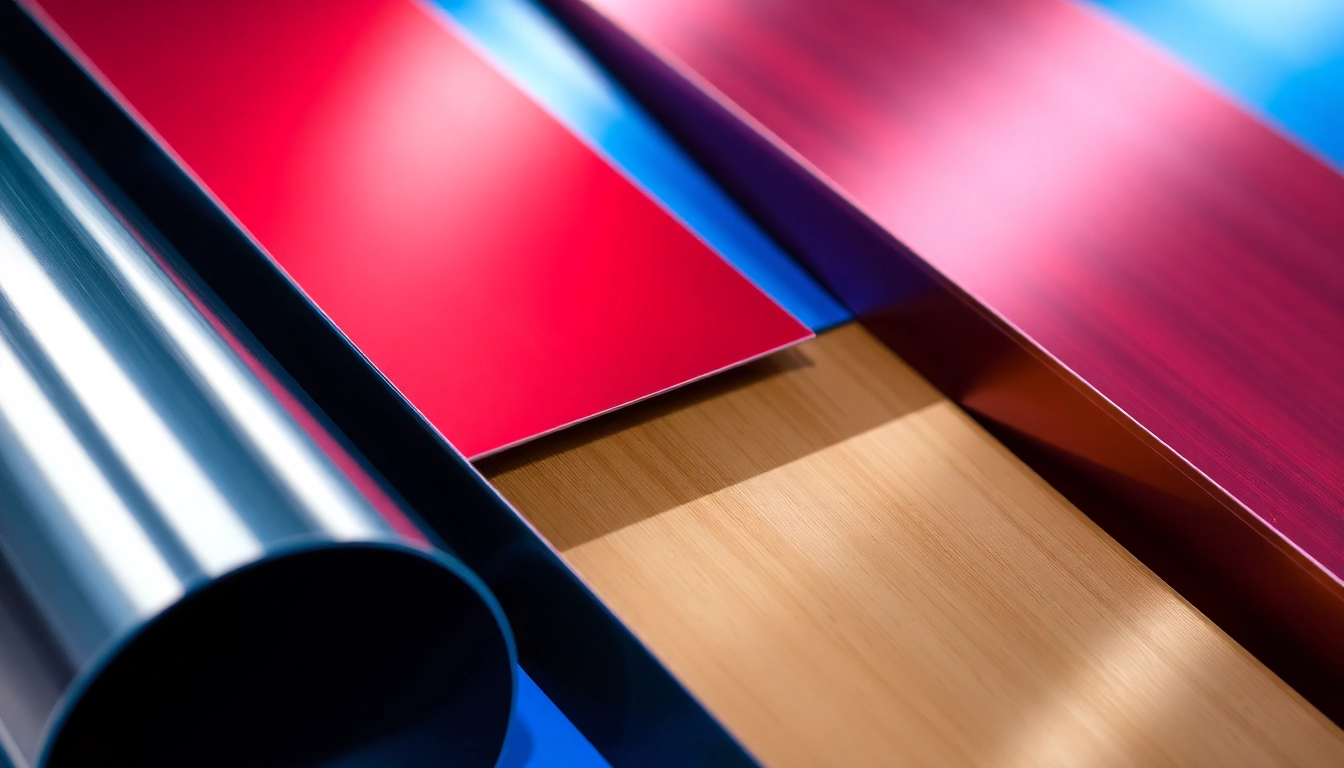
Essential Guide to Powder Coating: Benefits, Techniques, and Applications
Understanding Powder Coating
In the world of finishing processes, powder coating stands out as a durable, efficient alternative to traditional liquid paints. Its unique properties and application methods have made it a popular choice for various industries, from automotive to furniture manufacturing. This article delves deep into the intricacies of powder coating, exploring its mechanics, applications, advantages over traditional methods, and much more.
What is Powder Coating?
Powder coating is a dry finishing process that involves applying a free-flowing, dry powder to a substrate, typically metal. The process relies on an electrostatic charge to ensure the powder adheres to the surface. After application, the coated item undergoes a curing process in an oven, which causes the powder to melt and form a hard, adherent coating.
This technique not only enhances the aesthetic qualities of the finished product but also provides a protective layer against corrosion, impact, and other environmental factors. Unlike traditional paint, which is liquid and requires solvents, powder coating provides a more eco-friendly option due to reduced VOC emissions.
How Powder Coating Works
The powder coating process can be broken down into several key steps:
- Preparation: The item is first cleaned to remove any dirt, grease, or existing finishes. This often involves chemical cleaning, sandblasting, or power washing.
- Application: The powder is electrostatically charged and sprayed onto the item using a spray gun. The charged particles adhere to the grounded item, creating an even coat.
- Curing: The item is placed in an oven, where the powder melts and forms a continuous film. The heat allows the coating to cure, developing a strong, durable finish.
Common Applications of Powder Coating
Powder coating is widely used across various sectors for a multitude of applications:
- Automotive: Enhances the longevity and visual appeal of vehicle parts such as wheels, chassis, and frames.
- Architectural: Used in the finishing of windows, doors, and aluminum structures to provide weather resistance and aesthetic appeal.
- Appliances: Commonly found in kitchen appliances like refrigerators and microwaves, offering a durable and attractive exterior finish.
- Furniture: Applied on metal furniture to protect against scratches and rust while providing a sleek appearance.
Advantages of Powder Coating Over Traditional Paint
Choosing powder coating over traditional liquid paint comes with numerous benefits:
Durability and Resistance Features
One of the standout advantages of powder coating is its exceptional durability. The thick finish is more resilient to chipping, scratching, and fading than traditional paint. It also exhibits excellent resistance to corrosion, making it ideal for products exposed to harsh environments. The thermal and chemical resistance of powder coatings means that they endure better in conditions involving heat, moisture, and corrosive substances.
Cost-Effectiveness of Powder Coating
While the initial setup for powder coating equipment may be high, the long-term savings can be substantial. Powder coating processes are fast, and the overspray can be reused, leading to less waste and lower material costs. Additionally, the durability of the coating minimizes the need for frequent repairs or repaints, resulting in significant savings over time.
Aesthetic Benefits and Customization
Powder coating offers vast color options and finishing techniques, allowing manufacturers to achieve desired aesthetics without compromising durability. Options like metallic, matte, and textured finishes provide an opportunity for customization that enhances branding. With the ability to create custom colors and finishes, businesses can set their products apart in a crowded marketplace.
Types of Powder Coatings Available
The variety of powder coatings available allows for a range of finishes suited to different applications:
Metallic and Gloss Finishes
Metallic powders contain tiny metallic particles that create a shimmering effect. This finish is popular in the automotive and consumer products industries, as it enhances visual appeal. Gloss finishes offer a shiny appearance that is easy to clean and maintain, while matte finishes provide a softer, more subdued look.
Textured vs Smooth Coatings
Textured finishes are designed to hide imperfections and provide a unique surface feel, often used in industrial applications. Smooth coatings are preferable for achieving sleek, modern aesthetics but may require more thorough surface preparation to ensure quality adhesion.
Specialized Powder Coating Options
Several specialized powder coatings address specific needs, such as:
- High-Temperature Coatings: Designed to withstand extreme heat, suitable for components in engines and exhaust systems.
- Anti-Graffiti Coatings: Offer enhanced protection against vandalism and can be cleaned easily without damage to the underlying finish.
- Electrostatic Dissipative Coatings: Require in applications that necessitate control of static electricity in sensitive environments like electronics.
The Powder Coating Process: Step-by-Step
Understanding the powder coating process is essential for anyone looking to apply it in their projects. Below is a detailed breakdown of each step involved in this process.
Preparation and Pre-Treatment of Surfaces
The success of the powder coating process heavily relies on proper surface preparation. Common methods include:
- Deburring: Removing sharp edges and burrs from the surface.
- Cleaning: Using solvents, detergents, or mechanical methods to ensure the surface is free of contaminants.
- Phosphating: An optional chemical treatment to enhance adhesion and provide corrosion resistance.
Application Techniques for Powder Coating
After preparation, the application of powder is done using various methods:
- Electrostatic Spray: The most common technique where the powder particles are charged and attracted to the grounded surface.
- Dip Coating: Involves immersing the item into a container filled with powder and then removing it to allow powder adhesion.
- Fluidized Bed Coating: Used for larger items, where powdered coating materials are fluidized and the item is dipped into the fluidized bed.
Curing and Finishing Steps
Once applied, the coated object is placed in a curing oven, typically set between 350°F to 400°F (about 180°C to 200°C) for about 10 to 20 minutes, depending on the thickness of the coating. This process not only ensures that the powder melts and flows to form a smooth finish but also completes the chemical reactions that create a durable film.
Common Challenges and Solutions in Powder Coating
While powder coating offers many benefits, challenges can arise. Here’s a look at some common issues and proposed solutions.
Understanding Common Defects
Defects in powder coating can manifest in several ways, including:
- Orange Peel: A texture that resembles the skin of an orange, often caused by improper application or curing.
- Chalking: A white powdery residue that develops on the surface, typically due to UV exposure.
- Coverage Issues: Inconsistent application that leaves areas uncoated or unevenly coated.
Improving Adhesion and Color Consistency
Ensuring proper adhesion involves thorough surface preparation and control of environmental factors. Maintaining stable temperature and humidity levels during curing can improve color consistency. Conducting pretests for color matching and adhesion can also help in identifying issues before mass production.
Maintenance of Powder Coated Surfaces
To preserve the integrity and appearance of powder-coated surfaces, regular maintenance is essential. This includes:
- Cleaning: Regularly wash the surfaces with mild soap and water to remove dirt and prevent buildup.
- Inspection: Periodically check for signs of damage or wear, especially in outdoor applications.
- Repair: Address any chips or scratches promptly with touch-up coatings to prevent corrosion.