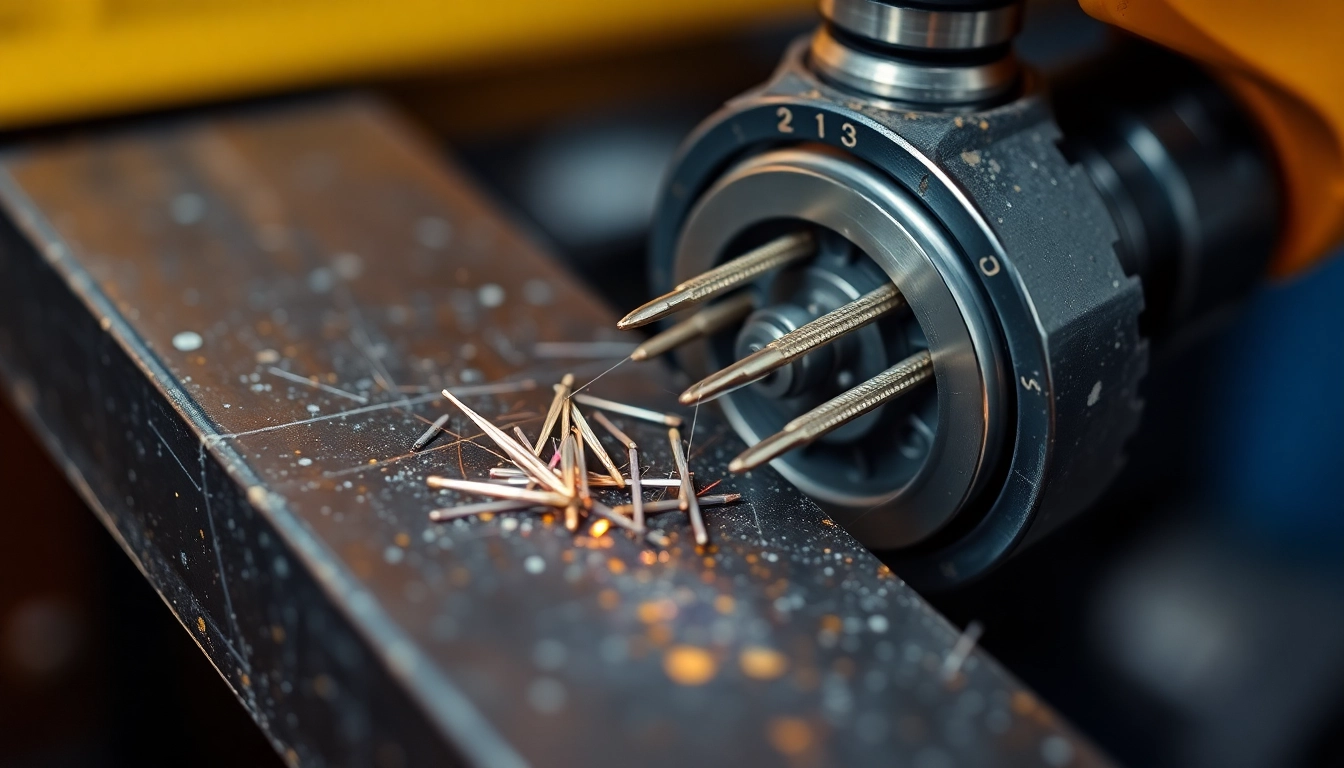
Essential Guide to Needle Guns: Maximizing Efficiency in Surface Preparation
Understanding Needle Guns
What is a Needle Gun?
A needle gun, often referred to as a needle scaler or needlegun scaler, is a powerful tool designed primarily for surface preparation. Its primary function is to remove rust, mill scale, and old paint from various metal surfaces. This tool operates by using multiple high-speed needles that rapidly oscillate, creating a hammering action that effectively dislodges stubborn contaminants. While the term “needle gun” might conjure images of firearms, in this context, it refers to a crucial tool in metalworking and maintenance applications. Needle guns are prevalent in automotive repair, shipbuilding, and various industrial sectors where metal surface restoration is essential.
How Needle Guns Work
Needle guns function through pneumatic or electric power, depending on the model. Pneumatic needle guns use compressed air to drive the needles, while electric versions use an electric motor. When activated, the needles move in rapid succession, creating a vibration effect that allows them to penetrate and break up rust, paint, and other undesirable materials from the metal surface. For example, a pneumatic needle gun typically operates at a rate of 3,000 to 6,000 blows per minute, making it exceptionally efficient for heavy-duty demolition and cleaning tasks.
The core mechanism consists of a series of steel needles mounted in a holder. As these needles oscillate, they impart significant energy to the surface contaminants, loosening them without damaging the underlying metal. The effectiveness of a needle gun can vary based on its design and the type of needles used, which can come in different shapes and sizes to suit varied applications. Additionally, the angle and speed at which the needle gun is used can impact its performance, requiring users to adjust their technique based on the task at hand.
Types of Needle Guns for Different Applications
There are several types of needle guns, each designed for specific applications:
- Pneumatic Needle Guns: These tools are favored in industrial settings due to their power and efficiency. They require a compressed air source, making them ideal for heavy-duty tasks like removing thick layers of rust from structural steel or marine applications.
- Electric Needle Guns: More portable and easier to use, electric needle guns are perfect for smaller-scale projects or environments where compressed air sources are unavailable. They are commonly used in automotive repair and light-duty tasks.
- Battery-Powered Needle Guns: These offer the ultimate convenience, eliminating the need for cords or air hoses. They are particularly beneficial for jobs in tight spaces or where mobility is a concern, though they may not provide the same level of power as their pneumatic counterparts.
- Heavy-Duty Needle Guns: Equipped with multiple needles and higher operating pressures, these models are designed for extreme conditions, such as removing heavy rust from industrial machinery or thick paint from large surfaces.
Benefits of Using a Needle Gun
Advantages Over Traditional Methods
Using a needle gun offers numerous advantages compared to traditional surface preparation methods, such as scrubbing or sanding. The key benefits include:
- Efficiency: Needle guns can complete tasks much faster than manual methods, saving time and increasing productivity, especially in large projects.
- Effectiveness: The rapid oscillation of needles can reach tight crevices and contours that other tools might miss, ensuring a thorough cleaning.
- Reduced Physical Strain: Operating a needle gun minimizes the physical effort needed compared to hand-held sanding or scraping, reducing fatigue and enhancing ergonomics.
- Less Damage: When used correctly, needle guns can clean surfaces without scratching or gouging the underlying metal, preserving its integrity.
Durability and Maintenance Considerations
Needle guns are typically built to withstand rigorous use, featuring rugged constructions with durable materials that can endure demanding environments. However, understanding their maintenance is crucial for prolonging their lifespan:
- Routine Cleanings: Regularly clean the needle gun and its components to prevent buildup of debris and dust, which can affect performance.
- Needle Replacement: Needles wear out over time. Monitoring their condition and replacing them as necessary ensures optimal performance.
- Lubrication: For pneumatic models, ensure proper lubrication according to the manufacturer’s guidelines to maintain efficiency and reduce wear.
Cost-Effectiveness in the Long Run
Investing in a needle gun may seem daunting due to its upfront cost, but it proves to be cost-effective over time. Consider the following:
- Time Savings: The ability to quickly prepare surfaces translates directly into lower labor costs, especially for commercial operations where time is money.
- Reduced Material Waste: Efficient surface preparation means less loss of material through damage during removal processes, reducing overall expenses.
- Longevity of Projects: Quality surface preparation ensures better adhesion for paints and coatings, leading to longer-lasting finishes and less frequent rework.
Choosing the Right Needle Gun
Key Features to Look For
When selecting a needle gun, several critical features should guide your decision:
- Power Source: Decide between pneumatic, electric, or battery-powered options based on your needs, work environment, and mobility requirements.
- Needle Count and Speed: Higher needle count and speed can improve efficiency; choose a model that matches the scale of your projects.
- Weight and Portability: Consider the tool’s weight and design for ease of handling, especially if you’ll be using it for extended periods.
- Noise Level: Some needle guns can be quite loud, so if you’re working in noise-sensitive areas, look for models designed to operate quietly.
Top Brands and Models Available
Several renowned brands manufacture quality needle guns, each offering various models to suit different needs:
- Chicago Pneumatic: Known for reliable pneumatic tools, their needle guns are robust and widely used in industrial settings.
- Ingersoll Rand: Offers a range of pneumatic tools, including needle scalers, lauded for high efficiency and durability.
- DeWalt: Their electric models are popular among DIYers and professionals alike for their portability and effective performance.
- Makita: Known for innovative electric solutions, their devices often feature ergonomic designs that enhance user comfort.
Comparing Electric vs. Pneumatic Needle Guns
Choosing between electric and pneumatic needle guns largely depends on your project requirements:
- Power and Performance: Pneumatic models generally offer more power and faster operation, suitable for heavy-duty tasks.
- Portability: Electric needles are often more portable and don’t require an air compressor but may sacrifice some power.
- Maintenance: Pneumatic models require more maintenance due to their air hoses and fittings, while electric models are usually less complex.
- Noise Levels: Pneumatic guns can be louder than electric ones, making the latter preferable for residential or noise-sensitive environments.
Best Practices for Needle Gun Use
Proper Handling and Safety Tips
Using a needle gun carries certain risks, so adherence to safety protocols is essential:
- Protective Gear: Always wear safety goggles, hearing protection, and gloves to shield against flying debris and noise.
- Secure Work Area: Ensure that the work area is clear from obstacles and that bystanders are at a safe distance.
- Read the Manual: Familiarize yourself with the manufacturer’s instructions and safety precautions before operation.
Maximizing Efficiency and Effectiveness
To achieve the best results while using a needle gun:
- Test on Scrap Material: Before attempting to clean critical components, test the machine on scrap material to gauge its effectiveness.
- Maintain the Correct Angle: Adjust the angle and distance from the surface to maximize the efficacy of needle penetration.
- Use Consistent Motion: Move the needle gun steadily across the surface to promote even cleaning and to avoid surface damage.
Common Mistakes to Avoid
Awareness of common pitfalls can help improve your needle gun usage:
- Excessive Pressure: Applying too much pressure can lead to damage. Let the tool do the work without forcing it.
- Ineffective Needle Selection: Using the wrong type of needles for specific tasks can lead to subpar performance. Always choose the correct needles based on surface hardness and project requirements.
- Neglecting Maintenance: Ignoring routine maintenance can shorten the lifespan of your needle gun and lead to decreased performance over time.
Maintenance and Troubleshooting
Regular Maintenance Tasks
Adopting a maintenance routine will enhance the performance and longevity of your needle gun:
- Cleaning: Regularly clean the needle gun’s exterior and its working parts to avoid dust accumulation that can impair functionality.
- Inspecting Components: Periodically examine the needles, hoses, and other components for signs of wear, replacing them as necessary.
- Lubrication: Follow the manufacturer’s guidance for lubrication, ensuring all moving parts operate smoothly.
Common Issues and Solutions
Even with proper maintenance, needle guns can experience problems. Here are some common issues and their respective solutions:
- Needles Getting Jammed: This may happen due to debris buildup. Ensure regular cleaning and inspection, and replace worn needles.
- Pneumatic Models Not Operating: If using a pneumatic model, check for air supply issues or blocked hoses. Ensure all connections are secure and free from leaks.
- Excessive Noise: If the noise level rises, inspect the tool for worn components or check that it is operating at the correct pressure.
When to Seek Professional Help
While many maintenance tasks can be performed by the user, certain situations may require professional assistance:
- Severe Performance Drops: If you notice a significant decline in performance despite maintenance, it may be time to consult with a technician.
- Internal Damage: If the tool has been dropped or subjected to excessive wear, professional evaluation can help identify internal issues.
- Complex Repairs: For issues involving electric wiring or internal pneumatic assembly, seeking professional help is advisable to ensure safety and effectiveness.