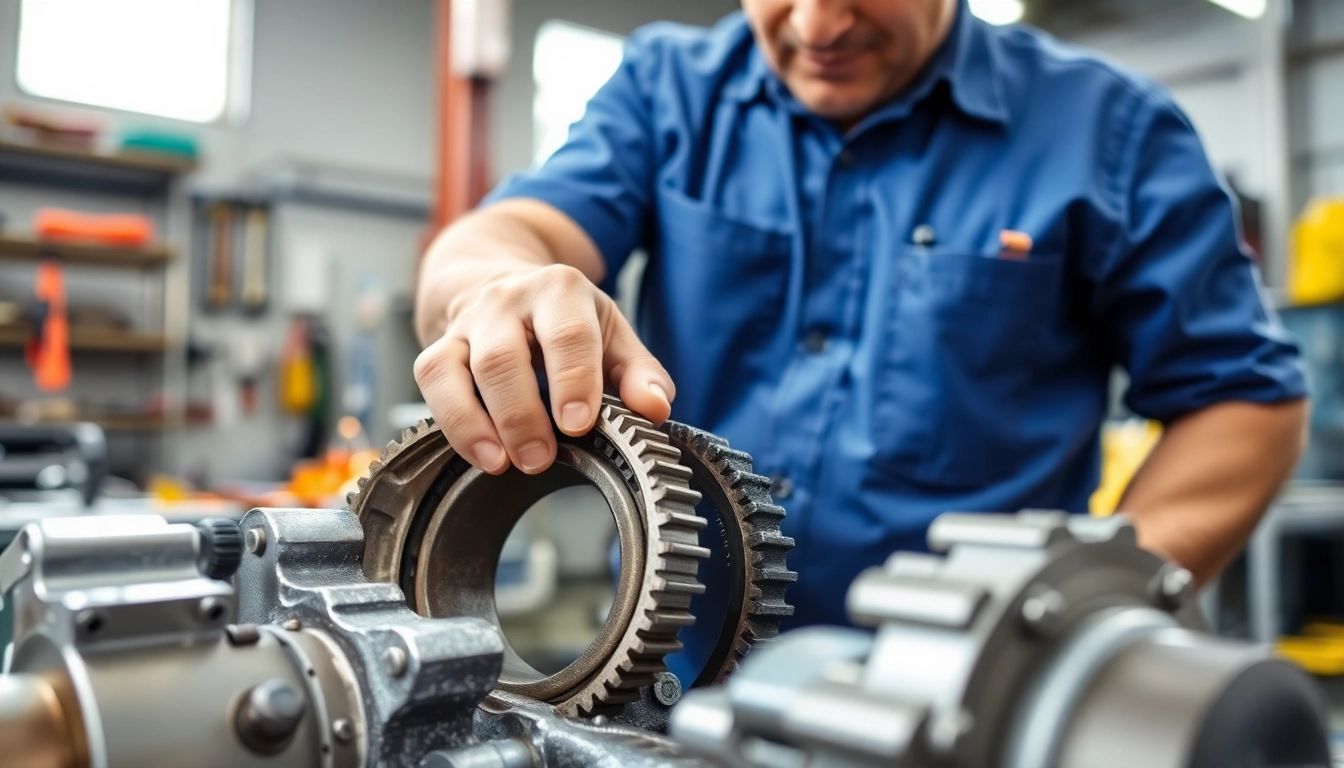
Essential Guide to Gearbox Bearing Replacement: Techniques and Tips for Success
Understanding Gearbox Bearings
Gearbox bearings are vital components in various machinery, ensuring smooth operation and optimal performance. These elements support shaft movement while reducing friction and wear, contributing to the efficiency and durability of mechanical systems. Understanding gearbox bearings, their types, and how they function is crucial for anyone involved in maintaining machinery. Proper knowledge also aids in the timely identification of issues, promoting effective gearbox bearing replacement when necessary.
The Role of Gearbox Bearings in Machinery
Gearbox bearings serve several essential roles in machinery. Firstly, they provide support for rotating shafts, allowing them to turn smoothly. This is crucial in applications ranging from automotive transmissions to industrial machinery. Secondly, they help absorb shock and vibrations, which protects other components from damage. Lastly, gearbox bearings play a critical role in reducing friction; less friction means lower energy consumption and less heat generation, which can lead to longer equipment life. In short, effective gearbox bearings are fundamental for efficient operation in any application, preserving the integrity of the entire mechanical system.
Common Types of Gearbox Bearings
Several types of gearbox bearings are commonly used, each designed for specific applications. Here’s an overview of some of the most prevalent:
- Ball Bearings: These are the most common type found in gearboxes, utilizing steel balls to reduce friction between moving parts.
- Cylindrical Roller Bearings: These bearings can support heavier loads and are ideal for applications requiring high radial load capacity.
- Spherical Roller Bearings: Designed to accommodate misalignments, these bearings are capable of handling both radial and axial loads.
- Tapered Roller Bearings: These bearings are suitable for applications where both radial and axial loads are present, making them ideal for gearboxes under significant stress.
Each type of bearing has specific advantages and applications, necessitating careful selection based on the machinery’s requirements.
Signs of Wear and Failure in Gearbox Bearings
Monitoring the condition of gearbox bearings is crucial for preventing unexpected failures. Here are several signs that bearing wear or failure may be imminent:
- Unusual Noises: Grinding, squeaking, or rattling sounds often indicate that bearings are failing.
- Excessive Heat: Overheating during operation can signal bearing fatigue or insufficient lubrication.
- Vibration: Increased vibration levels can highlight imbalance or bearing deterioration.
- Visible Damage: Cracks, dents, or discoloration on bearings can indicate serious wear, necessitating immediate attention.
Regular monitoring of these signs can help in proactively addressing issues, ensuring optimal performance and longevity of the machinery.
Preparing for Gearbox Bearing Replacement
Before proceeding with gearbox bearing replacement, it’s critical to prepare adequately. A well-thought-out approach will facilitate a smoother process and minimize complications.
Tools Required for Bearing Replacement
Proper tools are essential for efficiently executing gearbox bearing replacement. Here’s a list of tools you will typically need:
- Socket set
- Wrenches (both metric and imperial)
- Bearing puller
- Crown nuts and lock nuts
- Torque wrench
- Grease gun and compatible grease
- Cleaning supplies (degreaser, rags)
- Safety goggles and gloves
Having the right tools on hand will streamline the replacement process and ensure that tasks are performed correctly, ultimately saving time and effort.
Safety Precautions to Consider
Safety should always be a priority when working on machinery. Here are essential safety precautions to take:
- Wear Personal Protective Equipment (PPE): Always wear safety goggles and gloves to protect against potential injuries.
- Ensure Adequate Lighting: Work in a well-lit area to prevent accidents and ensure visibility of all components.
- Proper Lifting Techniques: Use appropriate equipment to lift heavy components, avoiding strain or injury.
- Lock Out/Tag Out Procedures: Ensure that machinery is properly shut down and locked to prevent accidental start-up during repairs.
By following these safety measures, you can minimize hazards and maintain a safe working environment throughout the process.
Identifying the Right Replacement Bearings
Selecting the correct replacement bearings is critical for ensuring optimal performance of the gearbox. Here are key considerations when choosing new bearings:
- Compatibility: Ensure that the replacement bearings match the specifications of the original components in terms of size, load rating, and material.
- Quality: Opt for high-quality bearings from reputable manufacturers to ensure durability and reliable performance.
- Operating Conditions: Consider the environment in which the gearbox operates (e.g., temperature, humidity, load cycles) to select appropriate bearing designs.
Research and consult specifications diligently to avoid future operational issues related to incorrect bearing selection.
Step-by-Step Gearbox Bearing Replacement Process
The process of replacing gearbox bearings involves several critical steps, each requiring careful execution.
Removing the Gearbox and Accessing Bearings
The first step in the replacement process is to remove the gearbox. Here’s how to do it:
- Shut Down the Equipment: Ensure that the machinery is off and all safety procedures are followed.
- Disconnect External Components: Remove any hoses, wires, or other connections attached to the gearbox to allow for full access.
- Unfasten the Gearbox Mounting: Use the appropriate sockets or wrenches to remove bolts securing the gearbox to the chassis.
- Carefully Remove the Gearbox: With stability in mind, lift the gearbox off its mounts, making sure to keep it level to prevent internal damage.
Once the gearbox is removed, you can access the bearings for replacement. Ensure that the work area is clean and organized before continuing.
Installing New Gearbox Bearings
Once the old bearings are removed, the installation of new ones is the next step:
- Clean the Bearing Housing: Use a degreaser to clean the housing thoroughly, removing any debris or old lubricant.
- Apply Grease: Coat the new bearings with the appropriate grease before installation to ensure smooth operation.
- Install Bearings: Carefully fit the new bearings into the housing, ensuring they are seated correctly and evenly.
- Reassemble the Gearbox: Follow the reverse order of disassembly to reattach covers and components, ensuring all parts are secured.
Proper installation is paramount for the effective functioning of the bearings and the overall gearbox.
Testing the Gearbox After Replacement
After the entire assembly has been reinstated, testing is crucial to validate the functionality:
- Initial Inspection: Check for any visible misalignments or loose bolts.
- Run the Equipment: Start the machinery and monitor its operation, listening for any unusual noises or vibrations.
- Check for Leaks: Ensure that there are no leaks from seals or connections.
- Temperature Monitoring: Observe the operating temperature of the gearbox during the initial run to ensure it remains within acceptable limits.
Conducting thorough tests will help validate that the bearing replacement was successful and that the machinery is back to optimal working condition.
Best Practices for Gearbox Maintenance
Preventative maintenance is key to prolonging the lifespan of gearbox bearings. Following best practices can save significant time and costs in the long run.
Regular Inspection and Maintenance Routines
Establishing a routine for inspection and maintenance can help catch wear and tear before they lead to complete failures. Consider implementing these routines:
- Scheduled Inspections: Create a calendar for regular inspections of gearbox bearings and surrounding components.
- Lubrication Management: Regularly check and replenish lubrication as needed to minimize wear.
- Vibration Analysis: Utilize vibration analysis technology to detect unusual patterns that could indicate problems.
Consistent monitoring can help you identify emerging issues and address them proactively.
Signs Indicating Further Maintenance is Required
Recognizing signs that additional maintenance is needed can be invaluable. Some indicators include:
- Unusual Noises: Persistent strange noises can suggest worsening bearing conditions.
- Increased Energy Consumption: A drop in efficiency may signal internal friction or mechanical issues.
- Frequent Heat Generation: Consistent overheating during operation indicates potential lubrication or bearing failure.
Paying attention to these signs can significantly reduce the risk of unexpected failures and the costs associated with emergency repairs.
Enhancing Lifespan of Gearbox Bearings
To prolong the life of your gearbox bearings, consider adopting the following measures:
- Quality Components: Invest in high-quality bearings that match your application’s specific needs.
- Controlled Operating Conditions: Mitigate environmental stressors and ensure that operational temperatures remain within limits.
- Effective Lubrication Practices: Implement proper lubrication strategies suited to the operating conditions to reduce wear and extend service life.
Maintaining an environment conducive to equipment longevity can translate to significant long-term savings and enhanced operational efficiency.
When to Seek Professional Help
Understanding when to solicit professional help is crucial for effectively managing gearbox issues. Some scenarios warrant professional intervention.
Assessing the Complexity of Gearbox Issues
Many gearbox problems can be diagnosed and remedied with basic knowledge and skills; however, certain complex issues may require experts:
- Severe Gear Damage: If gears or internal components show significant wear or damage, professional assessment is advised.
- Unidentifiable Symptoms: If you’re unable to ascertain the cause of unusual sounds or vibrations, seek expert diagnosis.
- Time Constraints: When time is a critical factor, professionals can often complete repairs faster due to their experience and resources.
Realizing when to engage professionals can save both time and money in mitigating further damage to the machinery.
Choosing the Right Mechanic for Gearbox Services
Selecting a qualified mechanic is essential to ensure high-quality service. Here are factors to consider:
- Experience and Reputation: Look for mechanics with proven experience, especially in gearbox repair.
- Certifications: Ensure that the mechanic holds relevant certifications to perform gearbox services professionally.
- Customer Feedback: Read reviews and feedback from past customers to gauge service quality.
Choosing the right professional ensures that repairs are conducted to a high standard, focusing on safety and efficiency.
Understanding Costs Associated with Professional Repairs
Understanding costs can help you budget effectively for necessary repairs. Consider the following:
- Service Fees: Mechanical shops often charge a base rate for their time and expertise.
- Replacement Parts: The cost of new bearings, gears, and other components needs to be factored in.
- Additional Repairs: Unforeseen issues may arise that require additional repairs, leading to increased costs.
Clear communication with your mechanic about expected costs ensures that you’re prepared for the financial aspect of repairs.