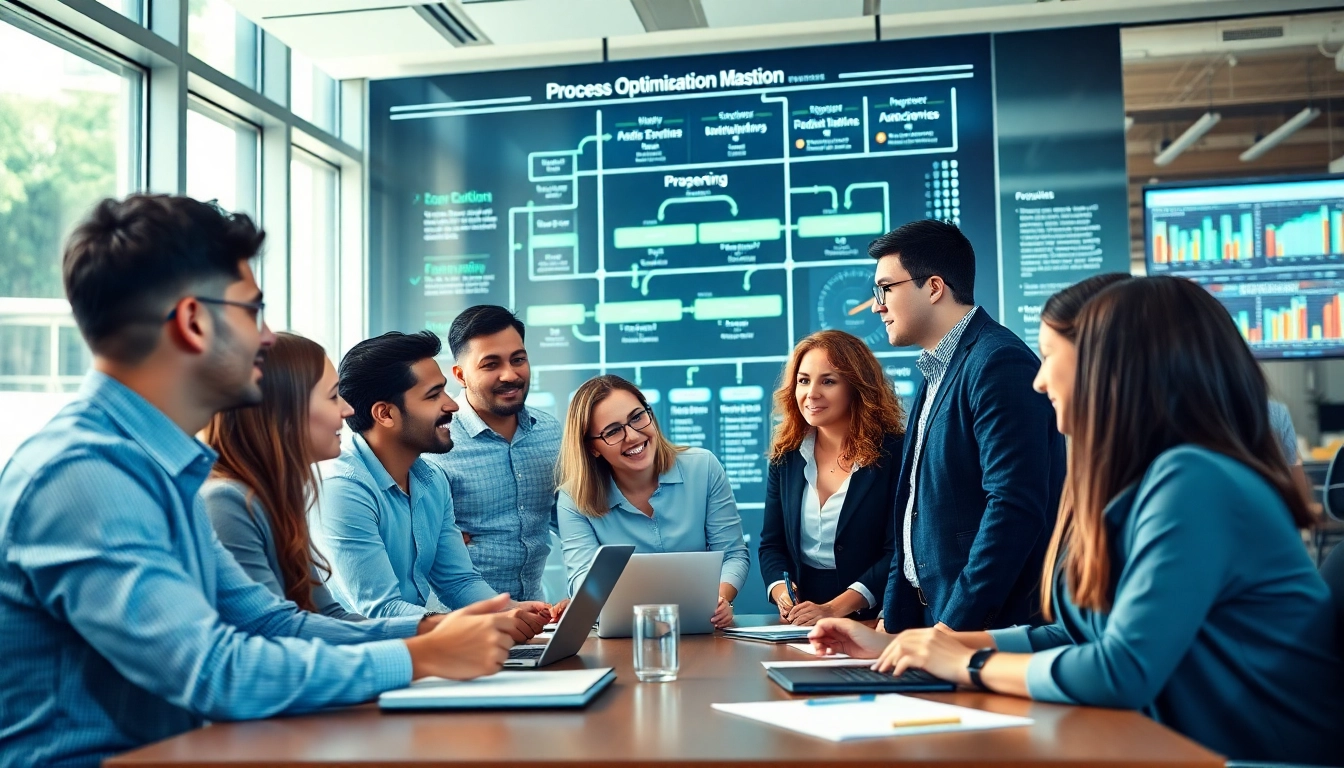
Enhancing Efficiency Through Effective Process Optimation Strategies
Understanding Process Optimation
What is Process Optimation?
Process optimation is the strategic approach of evaluating and refining a company’s operations to enhance efficiency, reduce costs, and improve customer satisfaction. This comprehensive method integrates elements of process management and quality assurance, ensuring that every step in a workflow is geared towards achieving maximum productivity. By focusing on details and eliminating inefficiencies, businesses can significantly transform their operational landscape. In today’s rapidly changing marketplace, mastering process optimation is not just beneficial; it’s essential for survival and growth.
Benefits of Process Optimation for Businesses
The advantages of process optimation extend across various domains within an organization:
- Improved Efficiency: Streamlining processes reduces time wastage and promotes smoother workflows.
- Cost Reduction: Less waste and optimized resource use lead to significant cost savings.
- Enhanced Quality: With standardized procedures in place, the quality of output improves, leading to higher customer satisfaction.
- Increased Agility: Companies can respond faster to market changes and customer needs, providing a competitive edge.
- Employee Satisfaction: A well-structured environment with reduced stress and workloads fosters a more satisfying work atmosphere.
Common Misconceptions about Process Optimation
Despite its clear benefits, several misconceptions hinder businesses from adopting process optimation:
- It’s Only for Large Companies: While larger organizations might have more complex processes, businesses of all sizes can benefit from optimizing their operations.
- It’s a One-Time Effort: Process optimation is an ongoing journey, not a one-time project. Continuous improvement is key to sustaining results.
- Focus Only on Technology: Though technology plays a vital role, process optimation also heavily involves people and culture.
- Only Relevant for Manufacturing: The principles of process optimation apply across industries, including service-based sectors.
Identifying Areas for Process Improvement
Analyzing Current Processes
A vital first step in process optimation is to conduct a thorough analysis of existing workflows:
- Map Out Processes: Create process maps to visualize workflows, identifying each step’s input, output, and interdependencies.
- Identify Bottlenecks: Look for areas where processes slow down or halt, often due to excessive handoffs or lack of resources.
- Assess Value Addition: Evaluate each process step to determine whether it adds value to the final product or service.
Key Performance Indicators to Consider
To effectively measure and analyze process performance, organizations should focus on specific Key Performance Indicators (KPIs):
- Cycle Time: The total time from the beginning to the end of a process, helping to identify delays.
- Throughput: The number of completed transaction outputs in a given time period, reflecting overall productivity.
- Defect Rates: Tracking errors or issues in output helps assess quality levels.
- Customer Satisfaction Scores: Direct feedback from clients can indicate how well processes meet demands.
Gathering Team Feedback and Insights
An essential aspect of process optimation is involving team members in the analysis phase. Here’s how to gather effective feedback:
- Conduct Surveys: Send out questionnaires focusing on current challenges and suggestions for improvement.
- Hold Workshops: Facilitate discussions where team members can brainstorm and address pain points.
- Encourage Open Communication: Create a safe environment for employees to speak up about inefficiencies they observe.
Techniques for Effective Process Optimation
Lean Methodology in Process Optimation
The Lean methodology focuses on value creation while minimizing waste. Companies can implement the following Lean techniques:
- Value Stream Mapping: Visualize product or service flows, identifying waste and areas for improvement.
- 5S Methodology: Sort, set in order, shine, standardize, and sustain to keep workspaces organized and efficient.
- Kaizen: Promote small, incremental changes rather than large-scale interventions to foster a culture of continuous improvement.
Utilizing Technology for Streamlined Processes
Technology enhances process optimation by automating tasks and providing real-time data. Consider the following:
- Automation Tools: Implement software to automate repetitive tasks, reducing errors and freeing employee time.
- Project Management Software: Use tools like Asana or Trello for better planning and coordination across teams.
- Data Analysis Platforms: Leverage big data analytics tools to glean insights from operational data, guiding optimization efforts.
Integrating Continuous Improvement Practices
Embedding a culture of continuous improvement ensures that process optimation efforts are not short-lived:
- Regular Review Meetings: Schedule periodic reviews to examine current processes and incorporate feedback.
- Benchmarking: Compare performance against competitors and industry standards to identify gaps and areas for enhancement.
- Training Sessions: Offer ongoing training on new practices and technologies to keep team skills relevant.
Measuring the Impact of Process Optimation
Establishing Success Metrics
To gauge the effectiveness of process optimation initiatives, organizations should establish clear metrics:
- Baseline Measurements: Analyze pre-optimization performance to understand the current state.
- Post-Implementation Metrics: Assess the same KPIs after implementing changes to see tangible results.
- Qualitative Assessments: Collect team and customer feedback on improvements and overall satisfaction.
Using Data to Drive Future Optimizations
Data-driven decision-making is crucial for sustained process optimation. Here’s how to leverage data effectively:
- Ongoing Data Collection: Continuously gather data to monitor process performance and reveal new challenges.
- Predictive Analytics: Employ data analysis techniques that help forecast potential issues and optimize resources accordingly.
- Trend Analysis: Identify patterns over time to inform future process adaptations and improvements.
Case Studies on Successful Process Optimation
Real-world examples of companies successfully implementing process optimation can provide valuable insight:
- Case Study 1 – Toyota: The automaker revolutionized manufacturing with the Toyota Production System, focusing on Lean principles. Resulting in significant cost savings and improved efficiency.
- Case Study 2 – Amazon: By leveraging technology and data analytics, Amazon has optimized its supply chain, leading to faster delivery times and higher customer satisfaction.
- Case Study 3 – Zara: The retail chain efficiently manages inventory control through a fast-fashion model, allowing for rapid response to market trends and customer demands.
Implementing Process Optimation Strategies
Step-by-Step Guide to Optimization
Here’s a structured approach to implementing effective process optimation:
- Define Objectives: Outline what the organization aims to achieve through process optimation.
- Map Current Processes: Build a baseline understanding of current operations to identify focal areas for improvement.
- Engage Stakeholders: Involve key personnel from various departments to gain a comprehensive perspective on processes.
- Develop an Action Plan: Formulate a detailed roadmap that outlines processes with assigned responsibilities and timelines.
- Implement Changes: Roll out specific iterations and optimizations, ensuring all team members are adequately trained.
- Monitor and Adjust: Regularly check on performance metrics and solicit feedback to make necessary adjustments.
Common Challenges and How to Overcome Them
Several challenges may arise during the optimation process, but they can be mitigated through proactive strategies:
- Resistance to Change: Address concerns through effective communication, demonstrating the value of proposed changes.
- Lack of Resources: Secure required investments by showcasing potential ROI through improved efficiencies.
- Siloed Departments: Foster cross-department collaboration to ensure unified objectives and shared insights.
Training Teams for Continuous Improvement
Building a culture centered on continuous improvement requires investment in team training:
- Train on New Tools: Regularly update team capabilities regarding new tools and technologies related to optimization efforts.
- Encourage Problem Solving: Foster a mindset where employees are empowered to identify issues and propose solutions.
- Incorporate Best Practices: Share success stories and best practices as part of ongoing training sessions to drive engagement.