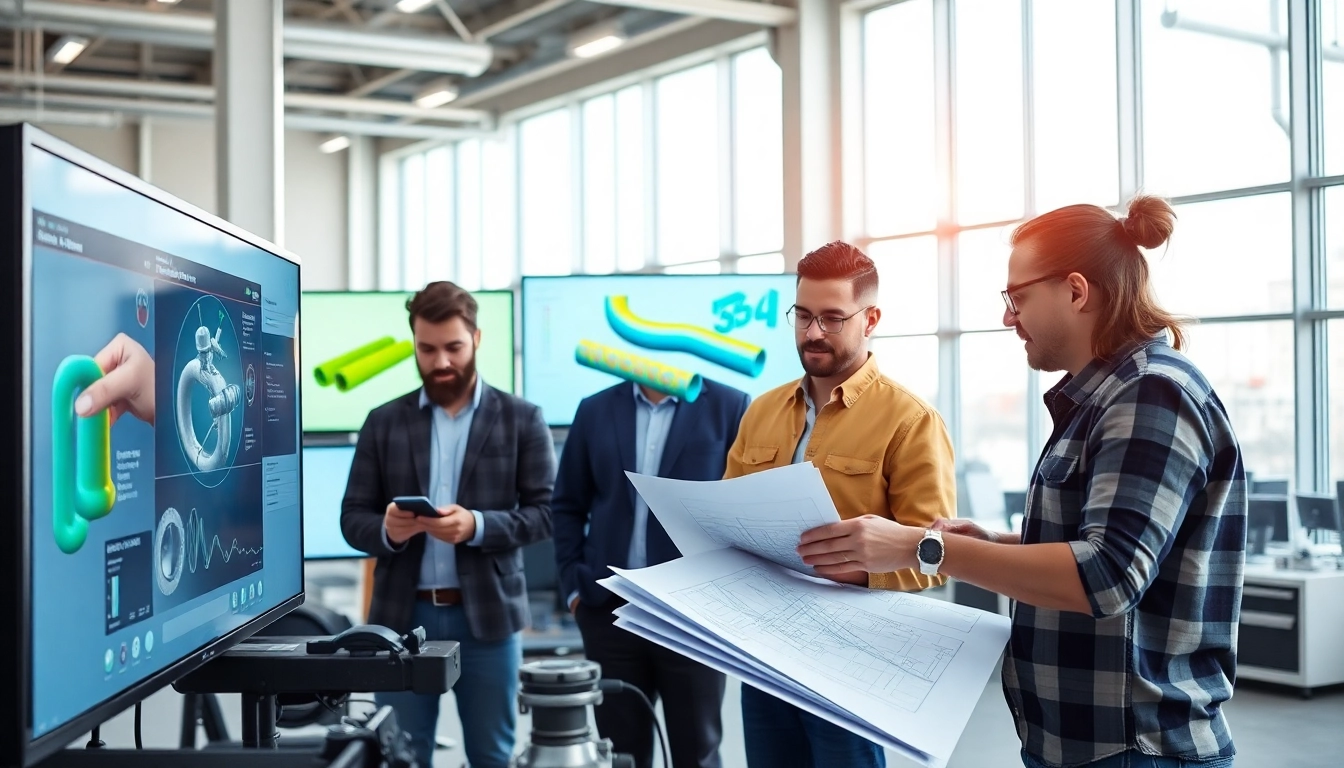
Maximizing Performance: Insights from a Leading Pipe Stress Company
Understanding Pipe Stress Analysis
What is Pipe Stress Analysis?
Pipe stress analysis refers to the engineering process used to determine the stresses, strains, and deformations that occur in piping systems due to various influences such as temperature changes, pressures, and external forces. The purpose of this analysis is to ensure the structural integrity and reliability of the piping systems throughout their operational lifespan. Engineers employ various techniques and software simulations to predict how different materials will react under various conditions and loads, ensuring that they can withstand normal operation and potential failures.
As operational demands increase and systems become more complex, the role of a pipe stress Company becomes critically important. With risks of pipeline failures leading to financial losses and safety hazards, a thorough understanding of how pipes behave under stress is essential.
Importance of Pipe Stress for Structural Integrity
The importance of pipe stress analysis cannot be overstated; it directly impacts structural integrity, safety, and efficiency in fluid transport. Piping systems that are not correctly analyzed may suffer from issues such as:
- Fatigue and Failure: Continuous strain or improper installation may lead to fatigue, resulting in cracks or complete failure, which can disrupt operations and require costly repairs.
- Water Hammer Effects: Sudden pressure changes can lead to shock waves that may damage pipes. Stress analysis helps in understanding these dynamics and mitigating risks.
- Thermal Expansion: Temperature fluctuations cause materials to expand and contract. If not accounted for, this can lead to misalignments causing wear and failures.
By prioritizing stress analysis, organizations can minimize unexpected failures, optimize maintenance schedules, and improve overall system reliability.
Common Methods Used in Pipe Stress Analysis
There are several established methods used in pipe stress analysis, each with its own merits:
- Finite Element Analysis (FEA): A computational technique that divides a structure into smaller, manageable elements to calculate stress and displacement. This method is particularly effective for complex geometries.
- Analytical Methods: Traditional calculations using mathematical equations often applicable to simpler piping systems. These methods are effective for straight pipes and standard configurations.
- Dynamic Analysis: This involves studying the effects of dynamic loads, like seismic effects, on piping systems, which can be crucial for structures in earthquake-prone areas.
Each method has specific applications and can be chosen based on the complexity of the piping system and the surrounding conditions.
Challenges Faced by Pipe Stress Companies
Technical Challenges: Accuracy and Simulation
Pipe stress companies face numerous technical challenges when conducting stress analysis. One of the most critical aspects is achieving accuracy in simulations. Inaccuracies can arise from various sources:
- Modeling errors including incorrect material properties and geometrical assumptions.
- Limitations in software tools that may not account for all real-world conditions.
- The challenge of harmonizing different data inputs and results to achieve a coherent analysis.
Thus, rigorous testing, validation, and the usage of enhanced simulation tools are necessary to mitigate these issues.
Regulatory Compliance Issues
Adhering to local and international regulations can be another complex challenge for pipe stress companies. Guidelines from organizations like ASME (American Society of Mechanical Engineers) dictate stringent requirements that must be met. Issues often include:
- Keeping up with frequently changing regulations that necessitate continual staff training and system updates.
- Proving compliance through documentation and analytical methodology, which can be time-consuming.
Thus, staying informed and compliant is crucial to avoid penalties and uphold the integrity of engineering practices.
Resource Management and Cost Efficiency
Effective resource management poses another challenge. Pipe stress companies often battle with the need to balance quality and efficiency while keeping costs manageable. Key considerations include:
- Maximizing workforce productivity without compromising safety or quality.
- Investing in advanced technologies that might seem cost-prohibitive initially but can lead to savings in the long run.
- Efficient project management to meet deadlines while ensuring thorough analysis.
Strategizing resources effectively allows for better financial outcomes and project success.
Best Practices for Effective Pipe Stress Management
Integrating Technology in Stress Analysis
Incorporating modern technology in pipe stress analysis is essential for accuracy and efficiency. Recommendations include:
- Utilizing state-of-the-art software that features advanced algorithms for precise modeling and analysis.
- Incorporating 3D modeling to visualize complex systems better and identify potential issues.
- Implementing real-time data monitoring for immediate feedback on system performance.
Technological integration enables better predictions and facilitates informed decision-making during engineering processes.
Regular Maintenance and Monitoring
Regular maintenance is fundamental to preventing problems related to pipe stress. Establishing a maintenance protocol entails:
- Scheduling routine inspections to check for wear and tear on piping systems.
- Utilizing predictive maintenance tools to anticipate and mitigate possible failures before they occur.
- Documenting all maintenance work to create a historical record, aiding future analysis.
Continuous monitoring is also necessary to ensure that systems operate within prescribed limits under varying conditions.
Collaboration Across Engineering Disciplines
Collaborating across various engineering disciplines can vastly improve the effectiveness of pipe stress management. This collaboration benefits projects by:
- Facilitating knowledge sharing between mechanical, civil, and structural engineers.
- Combining expertise leads to comprehensive systems analyses, considering all factors that may affect pipe stress.
- Improving project responses to unforeseen issues through streamlined communication processes.
By fostering a collaborative environment, engineering teams can develop robust solutions to complex engineering challenges.
Choosing the Right Pipe Stress Company
Evaluating Expertise and Experience
When selecting a pipe stress company, evaluating their expertise and track record is crucial. Key indicators of a reputable company include:
- A demonstrated history of successful projects, particularly within your industry.
- Certifications and licenses that attest to their adherence to industry standards.
- A skilled team with diverse experience, as varied expertise often leads to innovative solutions.
Engaging with experienced companies can significantly enhance project outcomes and mitigate risks.
Assessing Technological Capabilities
Assessing a company’s technological capabilities involves understanding the tools and processes they employ. Some important factors are:
- Do they utilize modern software for stress analysis and simulation?
- Are they equipped to conduct various analyses including dynamic simulations and seismic evaluations?
- Do they invest in ongoing training to ensure teams are up-to-date with the latest technology?
Choosing a company that prioritizes technology can enhance the efficiency and accuracy of pipe stress analyses.
Client Testimonials and Case Studies
Client testimonials and case studies provide insights into a company’s capabilities and reliability. When considering a contractor, look for:
- Detailed case studies that map the process from initial analysis to project completion.
- Positive client testimonials that speak to customer satisfaction and problem-solving abilities.
- Evidence of repeat business or partnerships, indicating long-term trust and satisfaction.
Such feedback can help prospective clients gauge the potential success of projects involving the company.
Future of Pipe Stress Analysis
Emerging Technologies in Stress Assessment
The future of pipe stress analysis looks promising with the advent of emerging technologies. Notable advancements include:
- Artificial Intelligence (AI): AI can enhance predictive analysis, enabling more accurate modeling of stress and strain under varying conditions.
- Internet of Things (IoT): IoT devices can monitor systems in real-time, providing invaluable data for continuous improvement and risk management.
- Virtual Reality (VR): VR can be utilized for training engineers and technicians, allowing for immersive problem-solving scenarios.
These innovations are set to revolutionize how assessments are conducted, improving efficiency and reliability.
Trends Shaping the Pipe Stress Industry
Several trends are currently shaping the pipe stress industry, including:
- Increased focus on sustainability and environmental impact, leading to stricter regulations and innovative materials.
- Growth in data analytics capabilities to enhance forecasting and diagnostics of potential failures.
- A shift towards modular construction methods, requiring adaptable stress analysis to cater to prefabricated systems.
Being aware of these trends will allow organizations to remain competitive and proactive in managing stress analysis projects.
Preparing for Future Challenges in Engineering Layouts
As engineering designs evolve, challenges will undoubtedly arise regarding pipe installations. Strategies to prepare for future challenges include:
- Adopting a proactive approach towards design flexibility to withstand changes in operational conditions and regulations.
- Encouraging interdisciplinary collaboration to better address the complexities of modern engineering projects.
- Investing in ongoing training and development for engineers to keep pace with emerging technologies and methodologies.
Embracing these strategies will position organizations to thrive amidst evolving challenges in the industry.