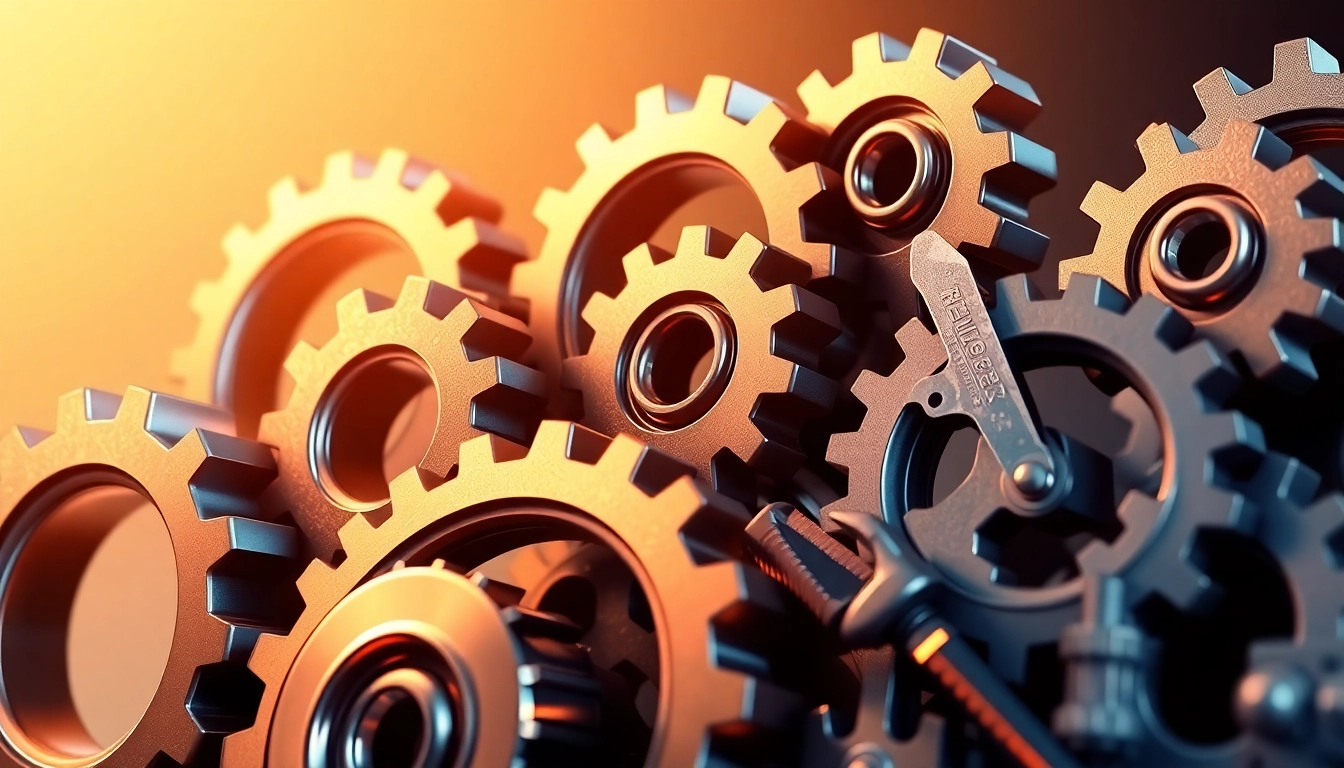
Enhancing Performance with byd Gears: Insights and Applications for Optimal Efficiency
Understanding byd Gears: Definition and Significance
What are byd Gears?
BYD Gears refer to gear systems specifically designed for various applications, particularly in engineering and manufacturing. These gears are critical components that aid in controlling the speed, torque, and direction of mechanical power transmission. Essentially, gears can be viewed as the heart of machines, converting rotational energy to achieve desired mechanical outputs. The effective functionality of byd gears ensures that systems operate smoothly and efficiently, whether it’s in automotive engineering, industrial machinery, or consumer appliances.
The Role of byd Gears in Engineering
In engineering, byd gears play an integral role in designing efficient machinery. They facilitate the transition of power between rotating shafts in a myriad of mechanisms, contributing to motion control, speed variation, and torque modulation. The importance of gear type selection in engineering design cannot be overstated as it directly impacts the efficiency and reliability of machines. For instance, in automotive engineering, the right gearing can enhance fuel efficiency while ensuring optimal power delivery from the engine to the wheels.
Common Applications of byd Gears
BYD gears find applications across diverse sectors:
- Aerospace: Gears are essential in aircraft systems, controlling flight mechanisms and improving aerodynamic efficiency.
- Automotive: In vehicles, gears manage power distribution from the engine to the wheels, affecting acceleration and fuel consumption.
- Manufacturing: In production lines, gears drive conveyor systems and automated machinery, enhancing productivity and operational reliability.
- Consumer Electronics: Gears within devices ensure precise movements, as seen in cameras and printers.
Types of byd Gears: A Comprehensive Overview
Spur vs. Helical byd Gears
When examining byd gears, two of the most fundamental types are spur gears and helical gears. Each comes with its unique applications and benefits:
- Spur Gears: Featuring straight teeth, spur gears are simple and cost-effective. They excel in transmitting power between parallel shafts. However, they can produce noise and vibration at high speeds.
- Helical Gears: These gears have teeth that are cut at an angle, which allows for smoother engagement and quieter operation. Helical gears are more efficient than spur gears at handling higher loads but can be more complex in design and manufacturing.
Bevel and Worm byd Gears: Unique Characteristics
Bevel and worm gears serve different functions in engineering applications:
- Bevel Gears: Designed to transmit power between shafts that are positioned at an angle to one another (most commonly at 90 degrees), bevel gears come in straight and spiral forms, helping to change the direction of rotation effectively.
- Worm Gears: Renowned for their ability to provide high torque reduction, worm gears consist of a worm (the screw) that engages with a worm wheel. They are particularly beneficial in applications requiring significant speed reduction and large load handling.
Choosing the Right Type of byd Gears
Selecting the appropriate type of byd gears depends on several factors such as load capacity, efficiency, noise levels, and the specific application requirements. Engineers must evaluate not only the mechanical properties but also the operating conditions like temperature, lubrication, and intended lifespan. A comprehensive analysis will yield gears that not only meet functional requirements but also provide greater reliability and efficiency.
Best Practices for Implementing byd Gears
Installation Techniques for Optimal Performance
The performance of byd gears heavily relies on proper installation techniques. Key steps include:
- Alignment: Ensure gears are properly aligned to prevent excessive wear and tear. Misalignment can result in inefficient power transmission and increase wear rates.
- Lubrication: Use appropriate lubricants to minimize friction and heat. Regularly monitor lubricant levels to ensure smooth operation.
- Torque Application: Adhere to specified torque settings when fastening gears to avoid stripping threads or damaging components.
Maintenance Tips for Longevity of byd Gears
Regular maintenance is vital for the longevity of byd gears. Consider the following best practices:
- Routine Inspections: Conduct periodic checks to identify wear signs such as cracks, abrasion, or unusual noise.
- Cleaning: Keep gears free from contaminants that may cause abrasions or hindrances in motion.
- Lubrication Schedule: Establish a systematic lubrication schedule, tailored to your specific operating environment, to preclude deterioration.
Common Mistakes to Avoid
When working with byd gears, avoiding certain pitfalls can save time and resources:
- Neglecting Specifications: Always adhere to manufacturer specifications regarding load, speed, and material recommendations. Failure to do so can lead to premature gear failure.
- Improper Lubrication: Using the wrong type of lubricant can significantly impact gear performance. Ensure selection aligns with operational demands.
- Overlooking Environmental Factors: Factors such as temperature, humidity, and dust can affect gear functionality. Adapt your systems accordingly.
Performance Metrics: Evaluating the Efficiency of byd Gears
Key Performance Indicators for byd Gears
Measuring the performance of byd gears requires specific indicators to track efficiency, durability, and overall effectiveness. Key metrics include:
- Load Capacity: The maximum load a gear can handle without failure.
- Efficiency: The ratio of output power to input power, indicating how well the gear converts energy.
- Wear Rate: The rate at which material loss occurs, affecting gear longevity and reliability.
How to Measure Gear Efficiency
To gauge gear efficiency, engineers typically use dynamometers and advanced software simulations, allowing for a comprehensive assessment of performance under various conditions. Efficiency measurements can help in troubleshooting mechanical issues and optimizing designs for future applications.
Improving Performance through Upgrades
Performance can always be boosted by upgrading existing gear systems. Engineers can focus on:
- Material Enhancements: Utilizing advanced composites or alloys to improve strength and wear resistance.
- Optimized Designs: Redesigning gear profiles for better load distribution and reducing stress concentrations.
- Incorporating Technology: Adopting modern manufacturing techniques such as 3D printing can create intricate designs that traditional methods may not achieve.
Future Trends in byd Gears Technology
Innovations in Gear Design
The future of byd gears is promising, with innovations poised to enhance performance and efficiency. Features like additive manufacturing allow for complex geometries that can improve strength-to-weight ratios, while advanced materials science is leading to stronger, lighter components that withstand more significant stress while maintaining efficiency.
The Impact of Smart Technology on byd Gears
Integration of smart technology into gear systems is becoming commonplace. Sensors can now monitor performance in real time, providing actionable insights that facilitate preventive maintenance and optimize operations. This technology enables predictive analytics to foresee operational requirements, mitigating downtime and fostering reliability.
Market Trends and Consumer Demands
The market is witnessing a shift toward sustainability, pushing manufacturers to produce efficient gear systems that minimize energy consumption and environmental impact. Consumer demand for electric and hybrid vehicles drives innovations in lightweight, energy-efficient gear designs. Companies are responding by investing in R&D to meet these evolving needs while staying competitive in a rapidly changing landscape.