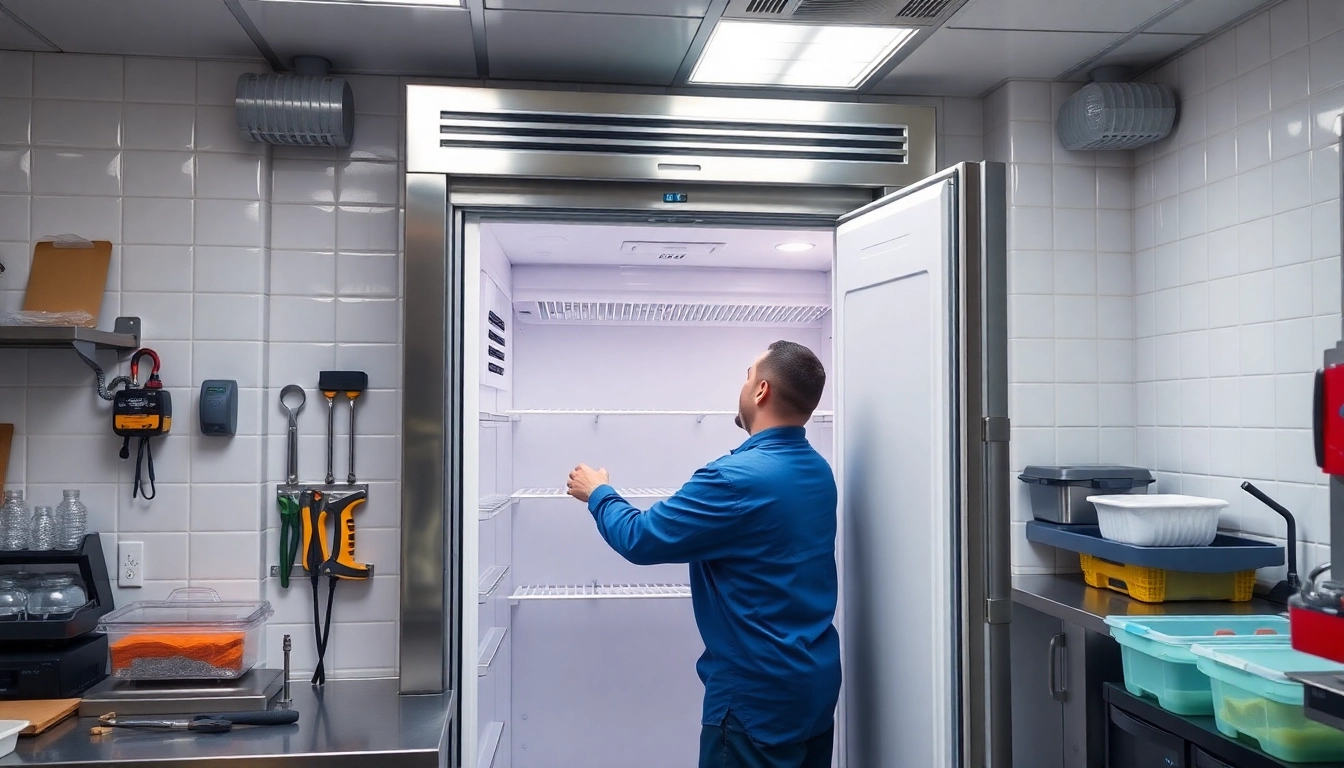
Expert Walk In Freezer Repair Services for Commercial Kitchens
Understanding Walk In Freezer Repair Needs
Maintaining the functionality and efficiency of a walk-in freezer is essential for any commercial kitchen or food storage facility. Whether you’re running a restaurant, grocery store, or distribution center, the uninterrupted operation of your refrigeration systems is critical. When issues arise, quick and effective walk in freezer repair becomes crucial to prevent loss of inventory or increased energy costs. In this section, we will delve into the common signs indicating a need for repair, the importance of timely maintenance, and how to identify qualified repair technicians.
Common Signs Your Walk In Freezer Needs Repair
Walk-in freezers are complex appliances that require proper monitoring to ensure they operate effectively. Several warning signs can help identify when your unit requires repair:
- Temperature Fluctuations: If the freezer is unable to maintain a consistent temperature, it can lead to spoilage of stored goods.
- Unusual Noises: Hearing unusual sounds such as grinding, clattering, or hissing can indicate mechanical issues, particularly with the compressor or fan.
- Frost Buildup: Excessive frost accumulation on walls or the evaporator coils can be a sign of airflow issues or a malfunctioning defrost system.
- Increased Energy Bills: A noticeable spike in energy costs may indicate that the freezer is working harder due to inefficiencies, often caused by underlying issues.
- Water Leaks: Puddles around the floor can point to drainage problems or other critical failures in the refrigeration system.
Importance of Timely Maintenance and Repairs
Neglecting timely maintenance can escalate small problems into costly repairs and potential equipment failure. Regular maintenance not only prolongs the lifespan of your walk-in freezer but also enhances its energy efficiency. Furthermore, proactive repairs can save businesses thousands by preventing inventory loss and ensuring compliance with health regulations. Scheduling routine inspections and fixing identified issues promptly can significantly reduce the risk of unexpected breakdowns.
How to Identify Qualified Repair Technicians
When searching for repair technicians for your walk-in freezer, it’s essential to choose professionals who are trustworthy and knowledgeable. Here are some tips to identify qualified technicians:
- Check Qualifications: Look for technicians with appropriate certifications and licenses, often including EPA Section 608 certification for refrigerants.
- Read Reviews: Investigate online reviews and ratings on platforms such as Google, Yelp, or local directories to gauge customer satisfaction.
- Experience Matters: Choosing technicians with significant experience in commercial refrigeration can help ensure effective troubleshooting and repairs.
- Ask for Referrals: Speaking to other local business owners about their experiences can help you find reputable service providers.
Cost Factors for Walk In Freezer Repair
The costs associated with walk-in freezer repairs can vary widely based on several factors, such as the nature of the repair, the equipment’s age, and the technician’s expertise. Understanding these cost factors is vital for managing your budget effectively.
Analyzing Repair Costs vs. Replacement
Deciding whether to repair or replace a malfunctioning walk-in freezer can be challenging. Some key considerations include:
- Age of the Unit: If the freezer is over 10 years old and frequent repairs are needed, replacement may be more cost-effective long term.
- Repair Costs: If repair costs exceed 50% of the value of a comparable new unit, replacement is typically advisable.
- Energy Efficiency: New models often offer enhanced energy efficiency features, reducing operating costs.
Breakdown of Common Repair Expenses
Typical repair expenses may include:
- Compressor Repairs: $250 to $650 depending on the issue.
- Evaporator and Condenser Cleaning: $100 to $300, critical for maintaining efficient cooling.
- Thermostat Replacement: Between $300 and $500, if recalibration isn’t sufficient to solve the issue.
- Door Seals Replacement: Averages about $200, but can range based on the freezer’s size.
Getting Quotes from Multiple Service Providers
When planning your budget for repairs, obtaining multiple quotes can provide insights into fair pricing for your service area. Ensure that quotes include a detailed breakdown of services and materials, and be wary of prices that seem significantly lower than the competition, as they may indicate subpar service or hidden costs.
Key Components in Walk In Freezer Systems
A well-functioning walk-in freezer relies on various components working in harmony. Understanding these components can empower business owners to make informed decisions when troubleshooting issues or seeking repairs.
The Role of Compressors in Freezer Functionality
The compressor is the heart of the refrigeration system, responsible for circulating refrigerant through the system. It compresses the refrigerant gas, increasing its pressure and temperature, before sending it to the condenser. A malfunctioning compressor can lead to temperature inconsistencies or complete failure of the unit. Signs of compressor issues include unusual noises and the inability to maintain set temperatures.
Understanding Evaporator and Condenser Functions
The evaporator coil absorbs heat from inside the freezer, facilitating cooling. Conversely, the condenser dissipates that heat outside. Both components must be adequately maintained to prevent issues like frost buildup or inefficient cooling. Regularly cleaning these coils and ensuring sufficient airflow around them is vital for optimal performance.
Essential Parts for Effective Repairs
Common repair parts necessary for walk-in freezer repairs include:
- Thermostats: Control the temperature. A faulty thermostat can result in an inability to maintain desired temperatures.
- Fan Motors: Ensure proper airflow. If fans fail, it can cause hot spots and frost formation.
- Door Seals: Crucial for maintaining internal temperatures. Worn seals can lead to significant air leaks, increasing energy costs.
Maintenance Tips for Extended Lifespan
Preventative maintenance is the key to ensuring your walk-in freezer operates efficiently and has a long service life. Adhering to a structured maintenance program can save time and money in the long run.
Routine Checks to Prevent Major Issues
Regularly scheduled checks should include:
- Temperature Monitoring: Regularly monitor and log temperatures to catch fluctuations early.
- Visual Inspections: Check for visible signs of wear and tear, such as rust, leaks, and unusual noises.
- Dust and Debris Removal: Maintain clean condenser and evaporator coils to enhance efficiency and prevent overheating.
Best Practices for Cleaning and Upkeep
Implementing best practices for cleaning your walk-in freezer can prevent many issues, including:
- Monthly Cleaning: Clean interior floors and shelving to prevent bacteria buildup and maintain sanitation standards.
- Regular Coil Cleaning: Use a soft brush or vacuum to remove dust from condenser coils bi-annually.
- Check and Replace Door Seals: Inspect seals for wear annually and replace them as necessary to maintain efficiency.
Scheduling Professional Maintenance Visits
In addition to routine checks, scheduling professional servicing at least once a year can help catch issues before they become significant problems. Technicians can provide a comprehensive assessment of the unit, including checking refrigerant levels and overall component function.
Emergency Walk In Freezer Repair Services
Issues with a walk-in freezer can happen unexpectedly, leading to critical situations that require immediate attention. Understanding when to call for help can minimize potential losses.
Identifying Emergencies: When to Call for Help
Recognizing emergency situations is crucial for safeguarding your inventory. Critical issues include:
- Temperature Rising Above Safe Levels: If temperatures climb beyond recommended levels, take immediate action to secure your products.
- Compressor Failure: If the compressor stops running altogether, immediate assistance is required to prevent spoilage.
- Power Loss: In the event of a power outage, extreme caution should be taken to monitor temperatures and respond quickly as needed.
Finding 24/7 Repair Services Near You
Having a reliable 24/7 repair service on hand is vital for businesses that rely on consistent refrigeration. Local directories, reviews, and personal recommendations can help identify quick-response services. When choosing a service provider, ensure they specialize in walk-in freezer repairs and have established a good reputation in your area.
Steps to Take Before a Technician Arrives
When facing an emergency, you can take several steps to prepare for a technician’s arrival:
- Document Issues: Keep a log of issues leading up to the failure, including temperature readings and unusual behaviors.
- Assess Inventory: Determine how much product is at risk and prepare a plan to mitigate inventory loss.
- Secure the Area: Ensure that the path to the freezer is clear for the technician’s access.